WEEK 15 & 16
MECHANICAL DESIGN
ASSIGNMENT DETAILS: Design a machine (mechanism + automation), including the end effector. Build the passive parts and operate it manually. Document the group project and your individual contribution.
/// FOR WEEK 15 - CLICK HERE ///
WEEK 16 - INTRODUCTION
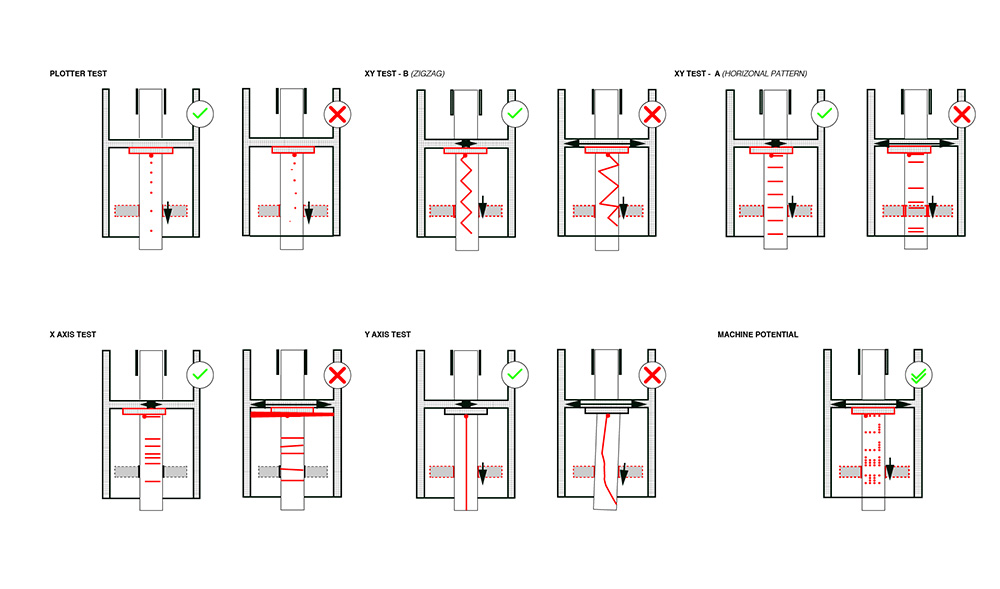
It was so satisfying to see our machine take shape but we were still only half way there. Now was time to work on the electronics and the coding. I made some diagrams to get a sense of what maybe this machine is capable of. We did not really use this diagram as we essentially never quite made it to such a testing phase. That would be possible if it was a 3 week assignment. I did what I could to help move us along by working on getting our machine up and running with Arduinos and Sparkfun Easy Drivers so that Marc could do the integration and, if possible, add his nicer electronics and finishing touches. We were so rushed and tired near the end that we lost a bit of our organizational effectiveness and things were a bit more complicated than they should have been but I think we managed nicely. Here are the items I worked on:
---> set up the EasyDriver motor drivers and the programming for the feed mechanism
---> make the electronics for the button controller
---> set up the EasyDrivers and initial programming for the x-axis
Here are some links I found useful:
http://blog.inventables.com/p/stepper-motors.html
http://www.schmalzhaus.com/EasyDriver/Examples/EasyDriverExamples.html
https://www.brainy-bits.com/homing-stepper-motor-at-startup/