INKSCAPE
Vector Drawing
I am most familiar with vector software like Adobe Illustrator which I use a lot to make concept sketches or to draw for machines in the Fab Lab but I have always wanted to learn more about Inkscape. At first glance, I find the Inkscape interface a little less intuitive but this is more likely an issue with my lack of familiarity with it. However, this is something I do consider when I am choosing a software to introduce kids to computer drawing. I have had success with software like Affinity Designer and Gravit Designer (which is free) and both are working iOS versions but lack some of the details that make working with machines easier. We always need to do a couple steps in Illustrator, Inkscape, or Corel Draw before sending drawings to a laser cutter. I know lots of artists and teachers using Inkscape and I have recently seen some of the unique features which make it a very interesting tool. Especially when you consider the active community surrounding it continually adding interesting features and add-ons.
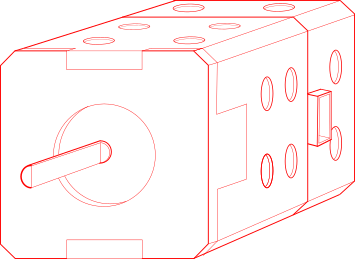
This is an initial concept sketch made with Inkscape to illustrate an idea for my final project. A stepper motor with a custom casing featuring mounting holes and a base containing a microcontroller running a version of Logo Programming.