THE BOARD
This board was one of the simpler options for the week. I took Neil's basic design and added a couple features. One was to make some traces that could later be used for NeoPixel output. The other was to make the board circular so that it could fit in the middle of a NeoPixel holder that I designed for the Molding & Casting week.
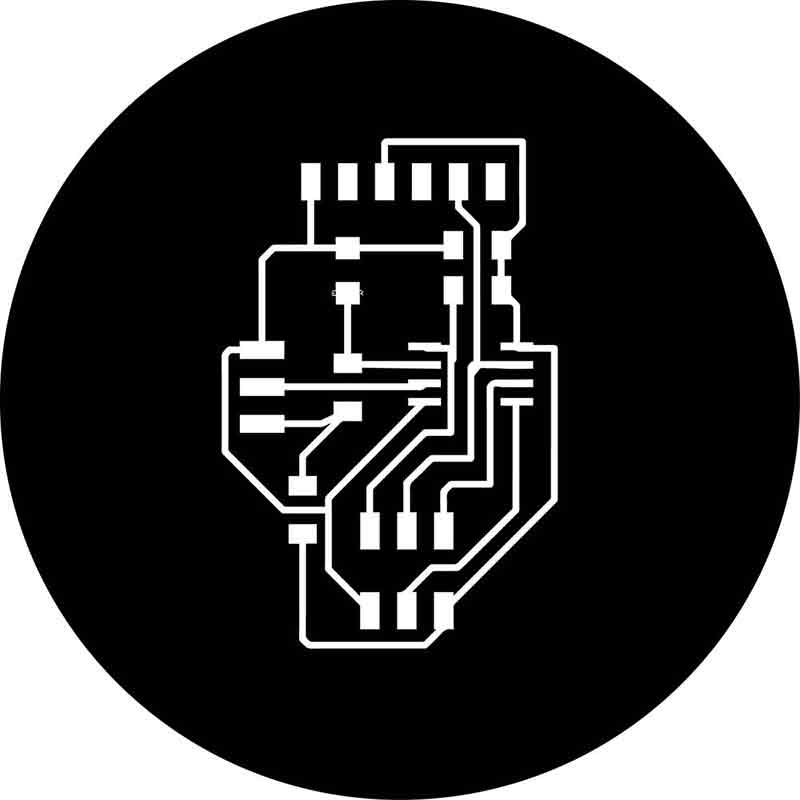
Because it was going to sit in the middle of this ring, I thought I would bend the FTDI pins so that they could stick out front.
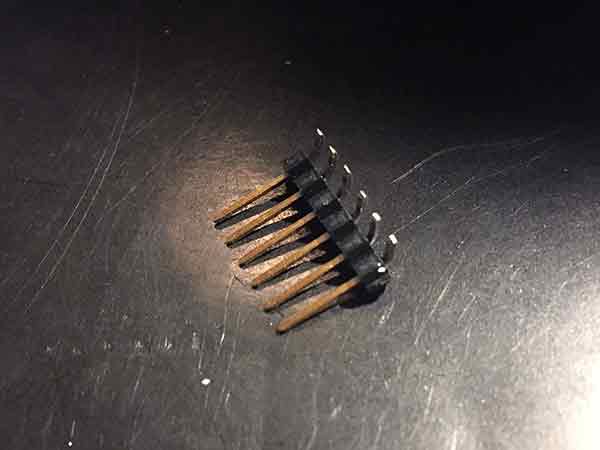
I took the traces and input them into mods. I used the default settings, PCB Traces 1/64 with 4 offsets.
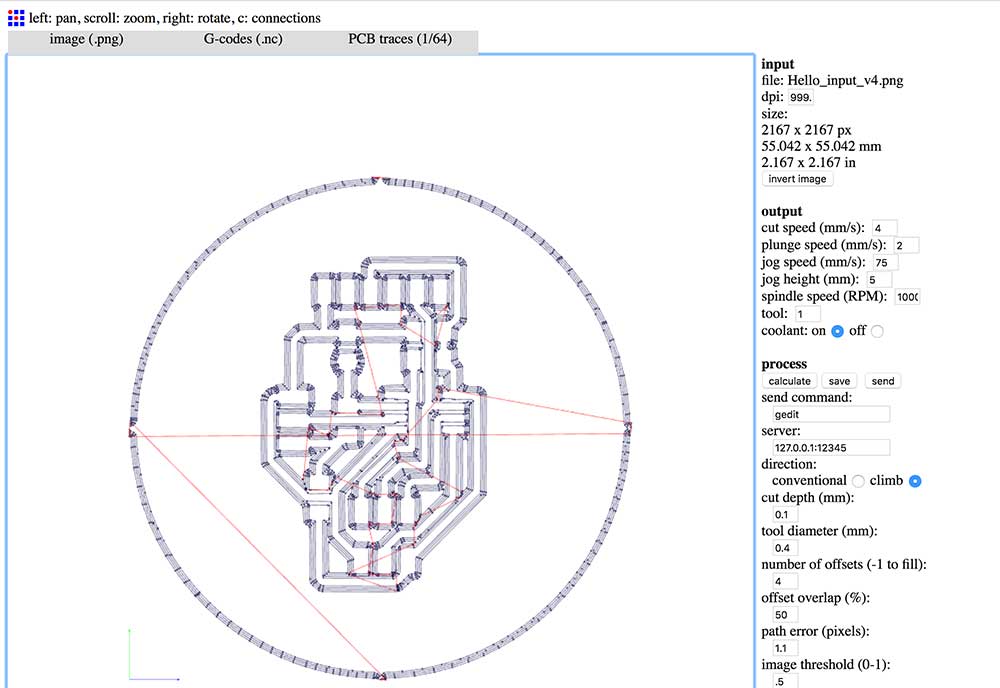
I used the mill at èchoFab with the same process I used in Week 5. Once the traces were milled, I had to switch the bit to cut out the perimeter of the circle. I moved the router away from the recently milled traces to have a look and accidentally pressed Reset Zero in Universal Gcode Sender. Oops! This reset the origin. I did not document this error but essentially, now it was going to be hard to cut the circle because I lost my place. Unlike a square shape with a defined corner, it was a lot of guess work. I was able to get it pretty close and I cleaned it up with sandpaper.
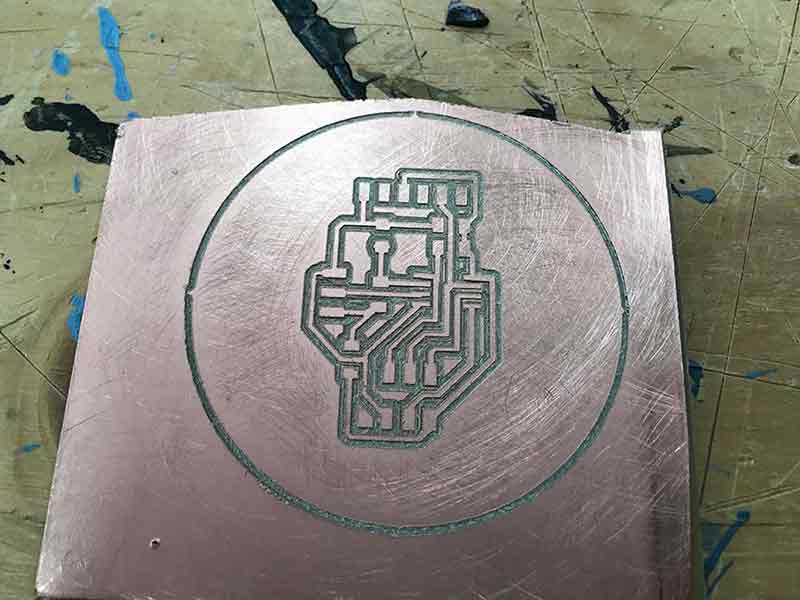
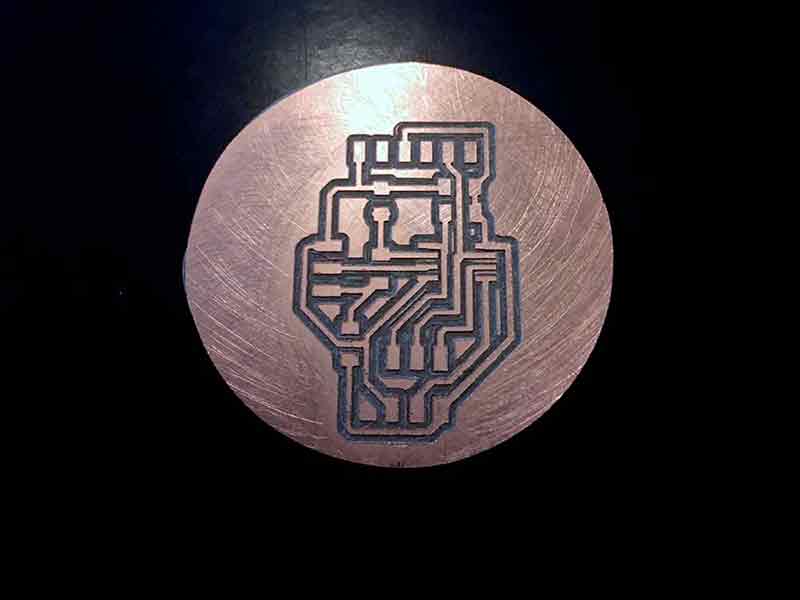
It didn't take a long time for the FTDI pins to rip off the board. It was a happy accident. It made me consider ways of getting the connectors out to the back of the board. I might end up doing this for my final project. If I don't have to, I would rather avoid adding Vias.
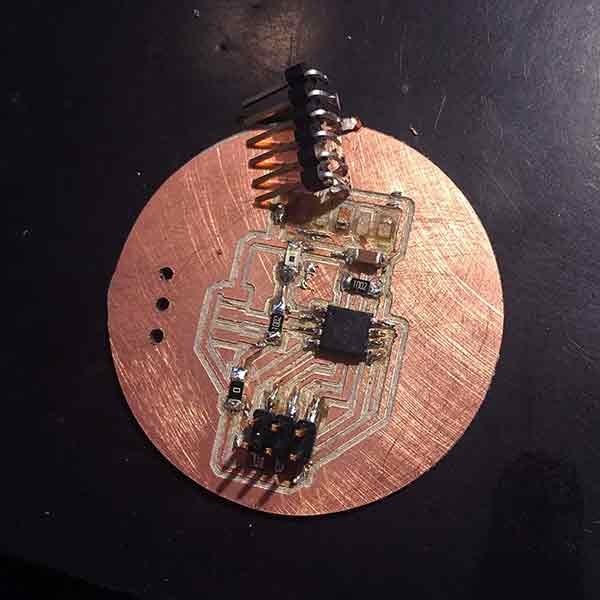
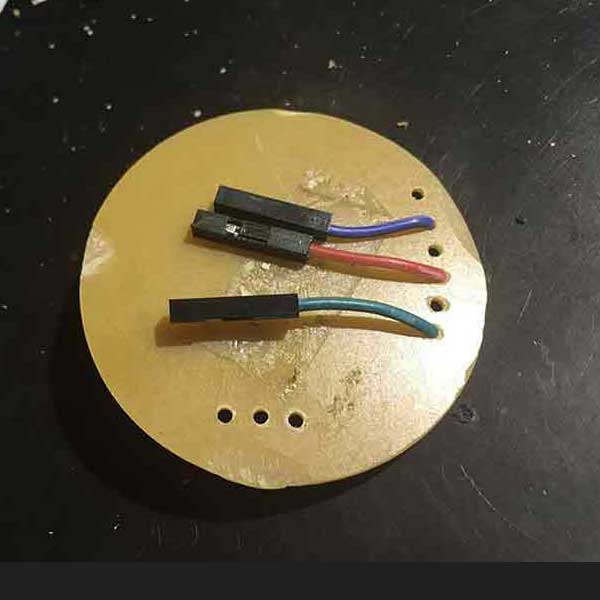
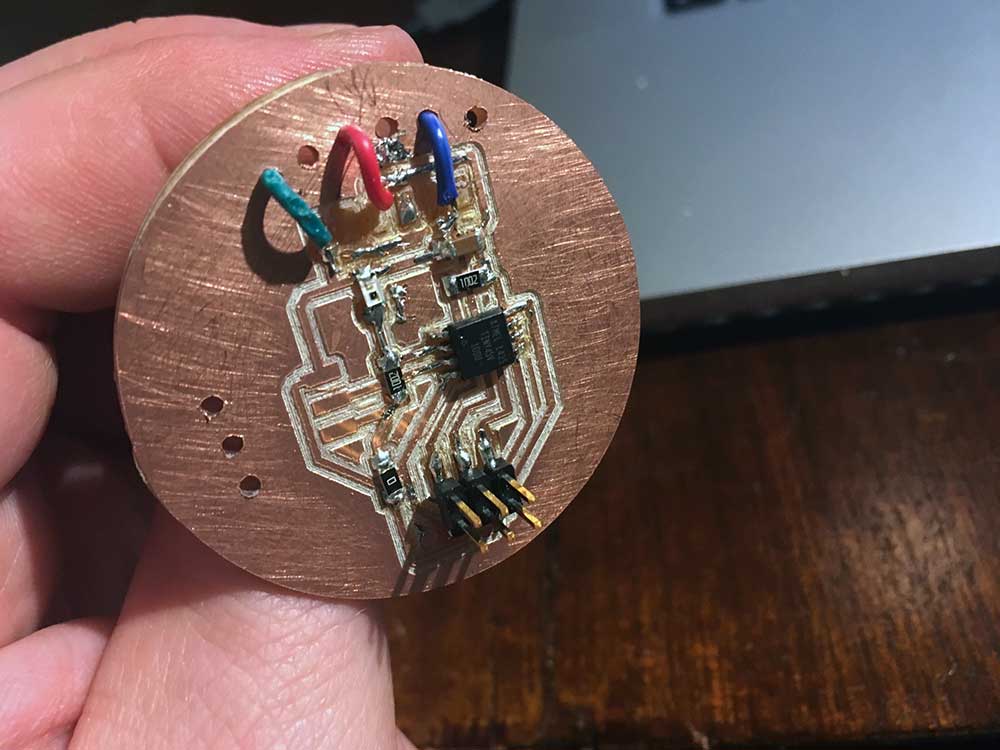
Once the board was ready it was time to load the program and test it out. I attached the usb to FTDI converter I had and my FabISP.
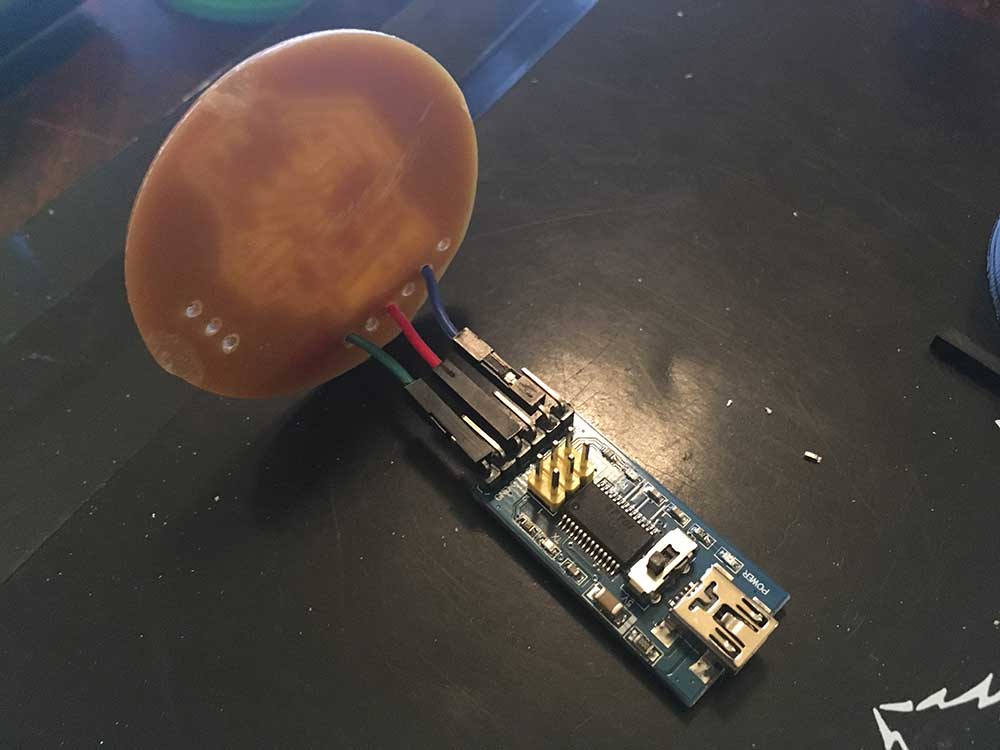
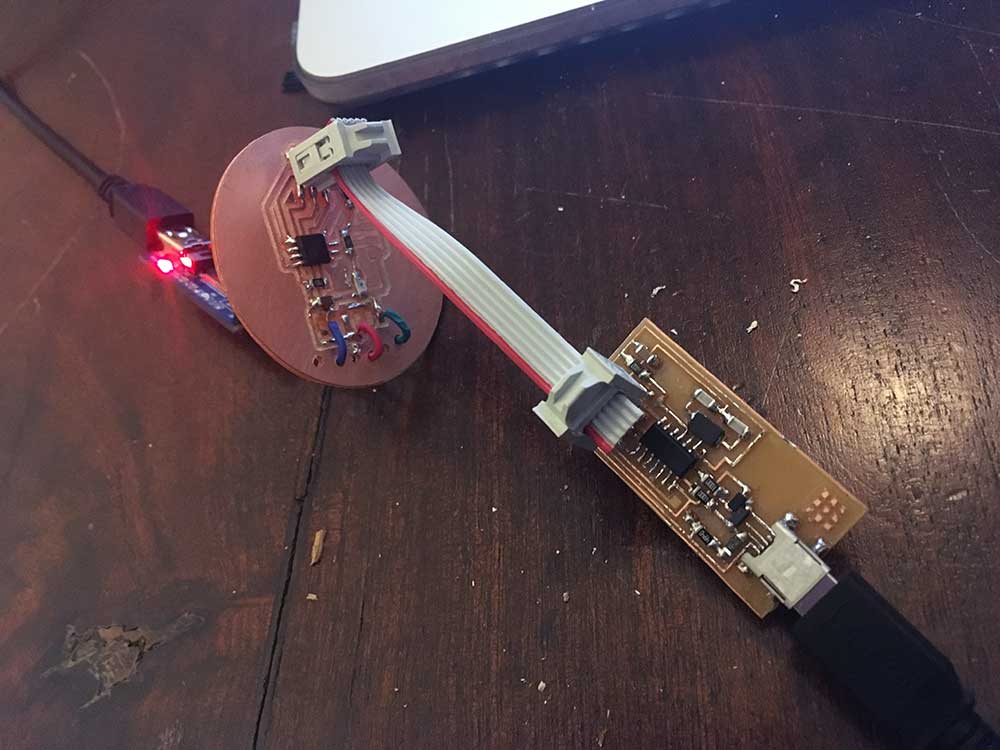
I copied Neil's Light sensor code from the Fab Academy input page into a folder on my computer. I navigated to the folder and used avrdude to generate the .hex file which I then pushed onto my board successfully.
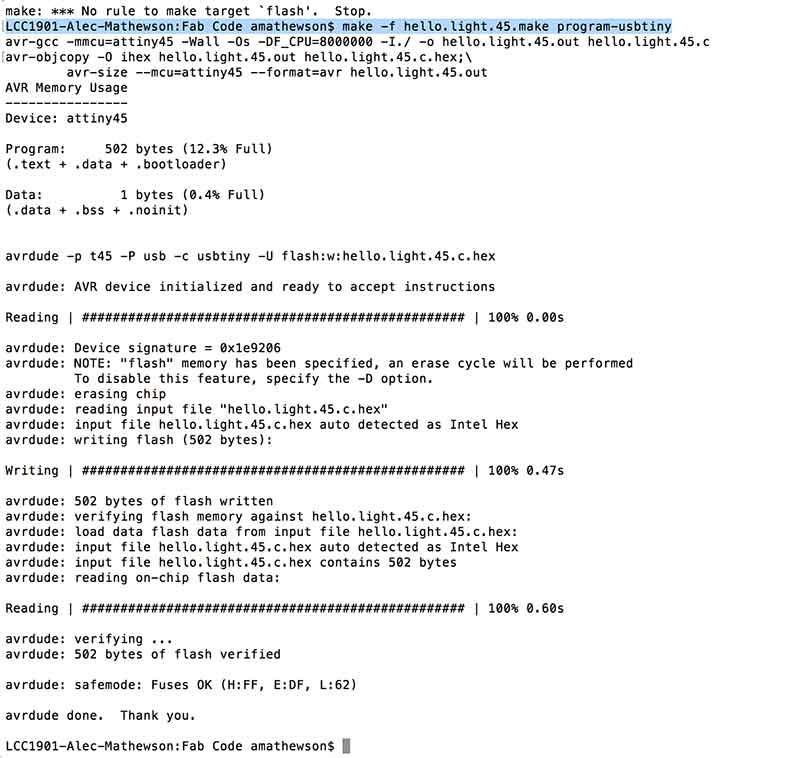