Machine
We are going to be using a TrotecSpeedy 400.
It has a working area of 1016 x 610 mm and the max x height of work piece is up to 305 mm depending on the table configuration an lens because focus distance is different for every lens.
If you are using this machine for the first time you can check this Operation manual.
The important steps to start:
Turn on the machine and the air extractor
Put the material on the table
Move the head over the material to find x/y position 0
Focus lens setting the distance from the material to the beam using the focus tool (if focusing manually)
Pressfit
We were there when some classmates tests the parameters for cutting the different materials so with that information we started right away with kerfs. We knew materials behave different and getting ahead of the third part of the assignment we decided to work with cardboard and mdf.
Cardboard
We started measuring the thickness of the material. For the cardboard it was 4.25 mm thick.
For this part we used Rhinoceros and used a circle to make the cuts. Firstly we put the exact size of the cardboard thickness, and from that we went up and down by 0.5 mm around the circle.
We opened the exported file in CorelDraw, but we had some issues with it, for some reason the numbers we put in order to know which gap had which measure weren't at the right place.
The other thing that happened to us is that went we sent it to print the scale was set for 2:1 even though our classmates were cutting in 1:1 right before us.
For the cardboard we found the best results with:
CUTTING
Power:100
Speed:0.6
Frequency:1000 Hz
ENGRAVING
Power:95
Speed:100
500 PPI
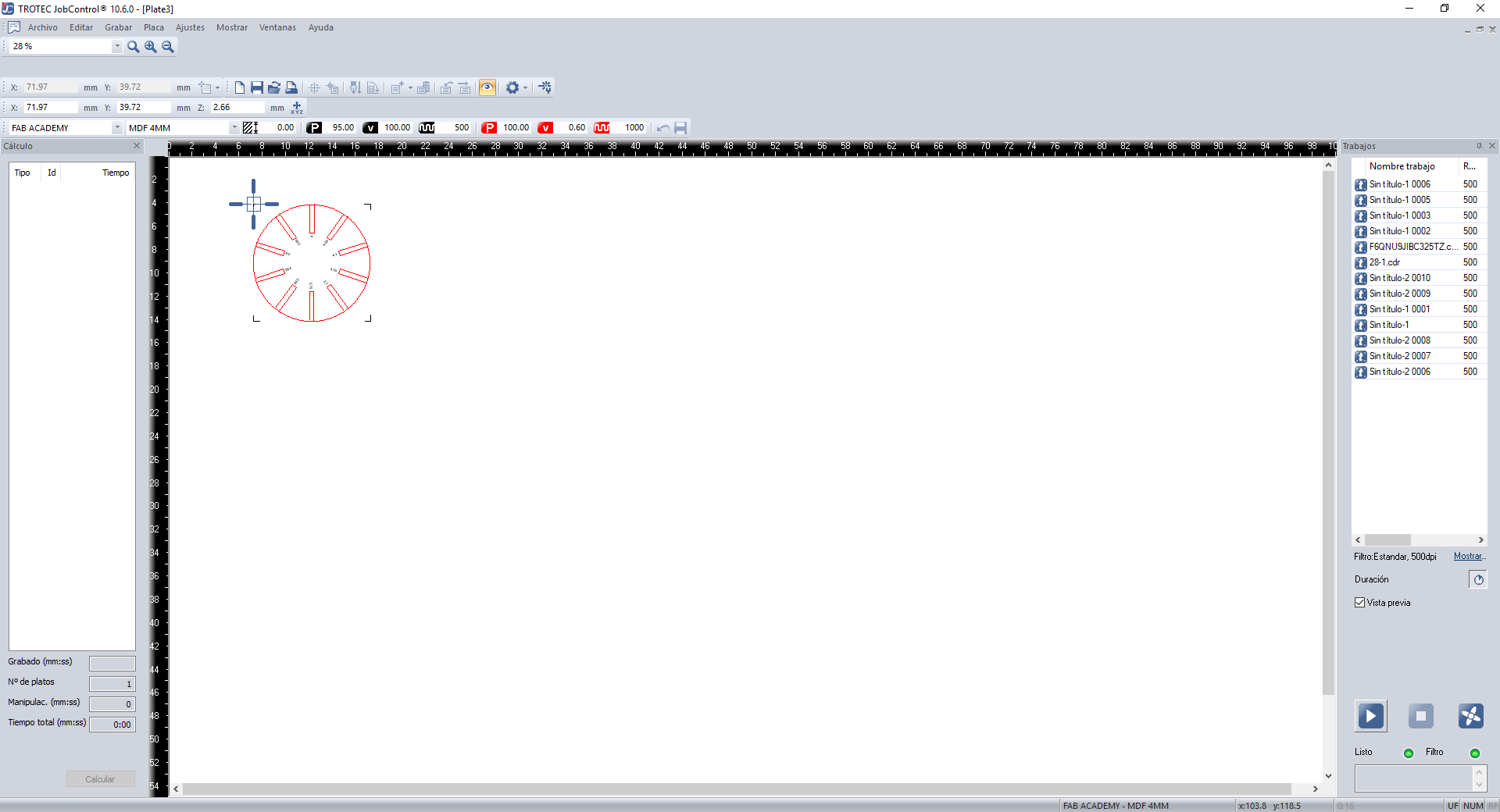
The gaps that were tight enough to hold the other piece were 3.95, 4 and 4.1 mm, however, although the 4.1 stayed in place, you could move it easily by pushing one of the pieces and not making any effort. Cardboard is a soft material so the results were not conclusive to us. We decided to start with MDF.
MDF
The mdf board had 4 mm thickness, and we proceeded the same as before with the cardboard.
For the parameters we sticked to this:
CUTTING
Power:100
Speed:0.5
Frequency:1000 Hz
ENGRAVING
Power:100
Speed:60
500 PPI
For our first cut, I pushed the piece a little and it came out easily, but the next pieces were not coming right, we had to reduce the speed to 0.4. It was weird but this was because the lens and the mirror inside the beam were very dirty after all the tests our classmates were making. After cleaning them we could cut again the MDF with 0.5.
What I learned
The kerf or the measure we should consider for what we want to make really depends on what do we want and how do we want it to behave.
IF you want a good joint that you can assemble and disassemble you can use a use a tolerance of 0.10 to 0.15 mm, this means reducing the wideness of the gap by 0.10 to 0.15 mm If you want a strong joint you can apply a 0.2 mm tolerance, this tolerance will work with just a little pressure.
We tried the different gaps and actually used the 3.75 mm gap for a 4 mm MDF. As you can see we were not able to separate the two pieces. You can force two pieces to join and then never separate, but you need to be careful with the material you are using because if you force it to fit, it may broke, as for example a thin plywood.
download
Laser tests - Dwg file