Week 10
Machine Week - Fab Lab Reykjavík & Fab Lab Vestmannaeyjar
Róbert Hreiðar Pálsson - Reykjavík
Gabríella Kamí Árnadóttir - Reykjavík
María Fönn Frostadóttir - Vestmannaeyjar
Mechanical Design & Machine Design
Group Assignment
- Actuate and automate your machine
- Document the group project and your individual contribution
Actuate and automate your machine
The Fab 2024 Saucemaster Ultimate Pro Max Assistive Condimental Saucing Technology 3000
Closeup video of machine working
Machine Construction
Beehive axes
The Fab 2024 Saucemaster Ultimate Pro max Assistive Condimental Saucing Technology 3000 or T.F.2.S.U.P.M.A.C.S.T 3000 is a single axis machine based on the Beehive project by Quentin Bolsee.
All the parts for the string-carried linear axis were downloaded from the Beehive Axes project repo and printed on a MK3 Prusa 3d printer. The parts were assemebled and a kevlar thread was used to carry the load. The axis was actuated by a stepper motor and a driver board.
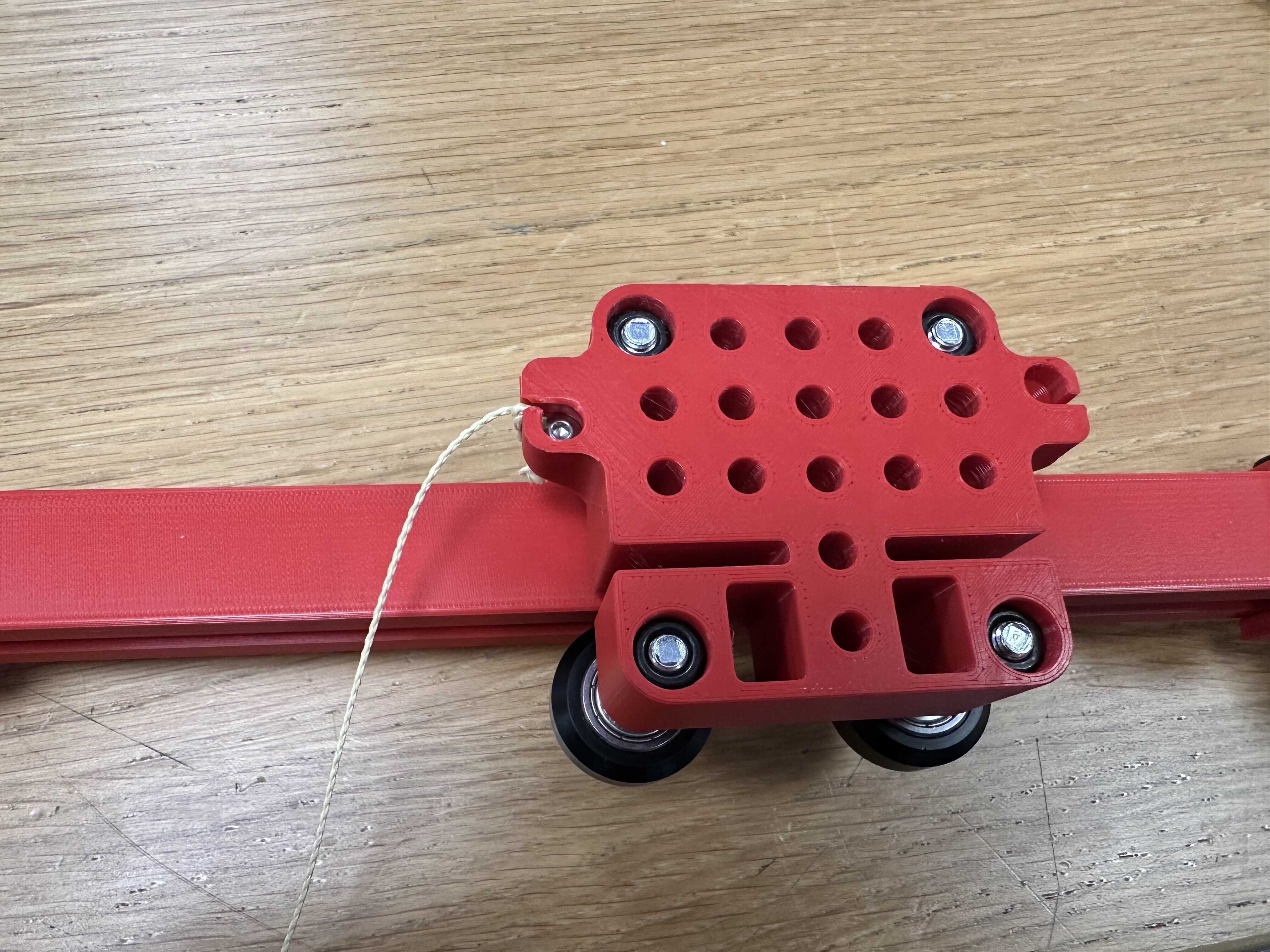
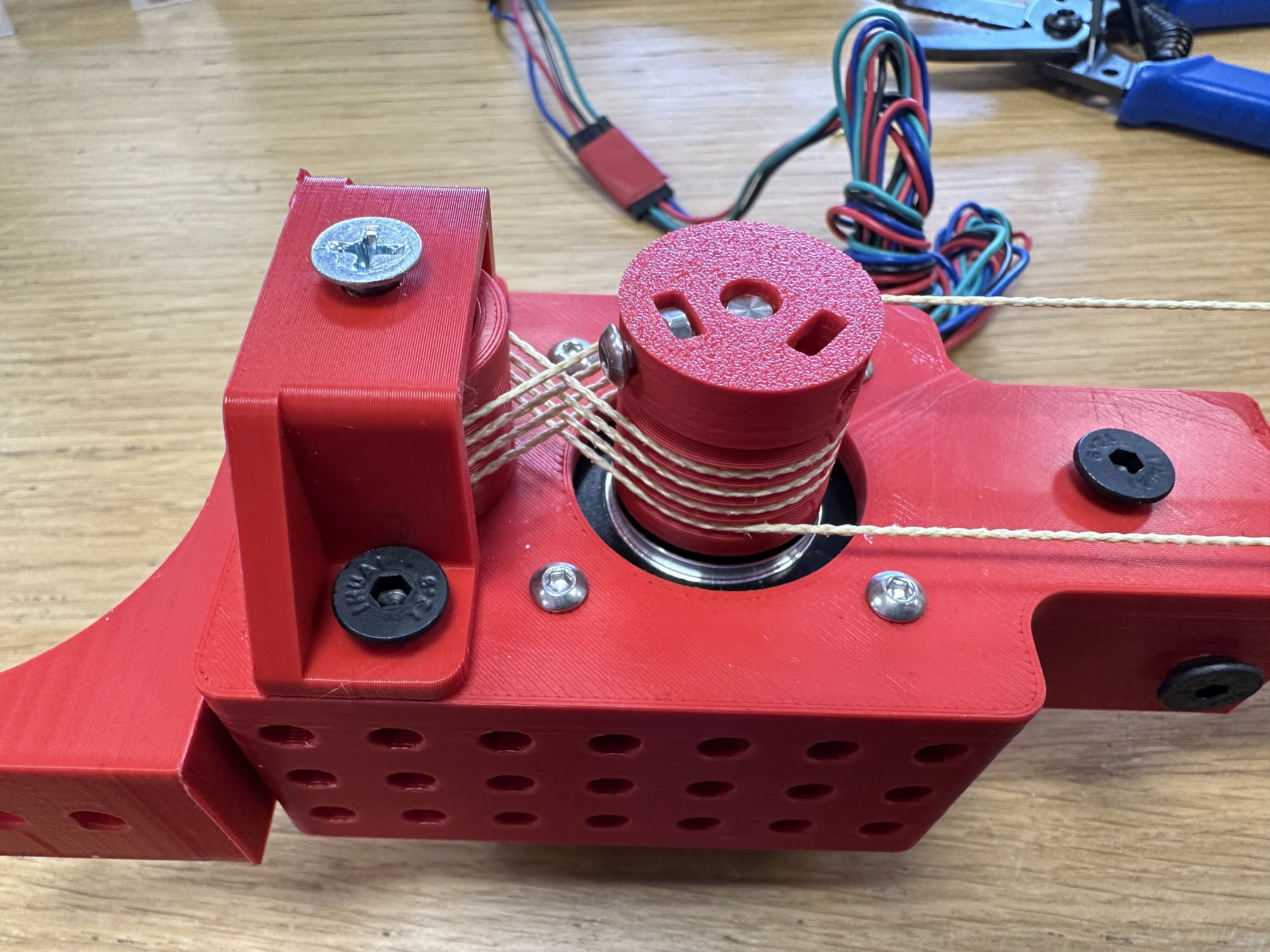
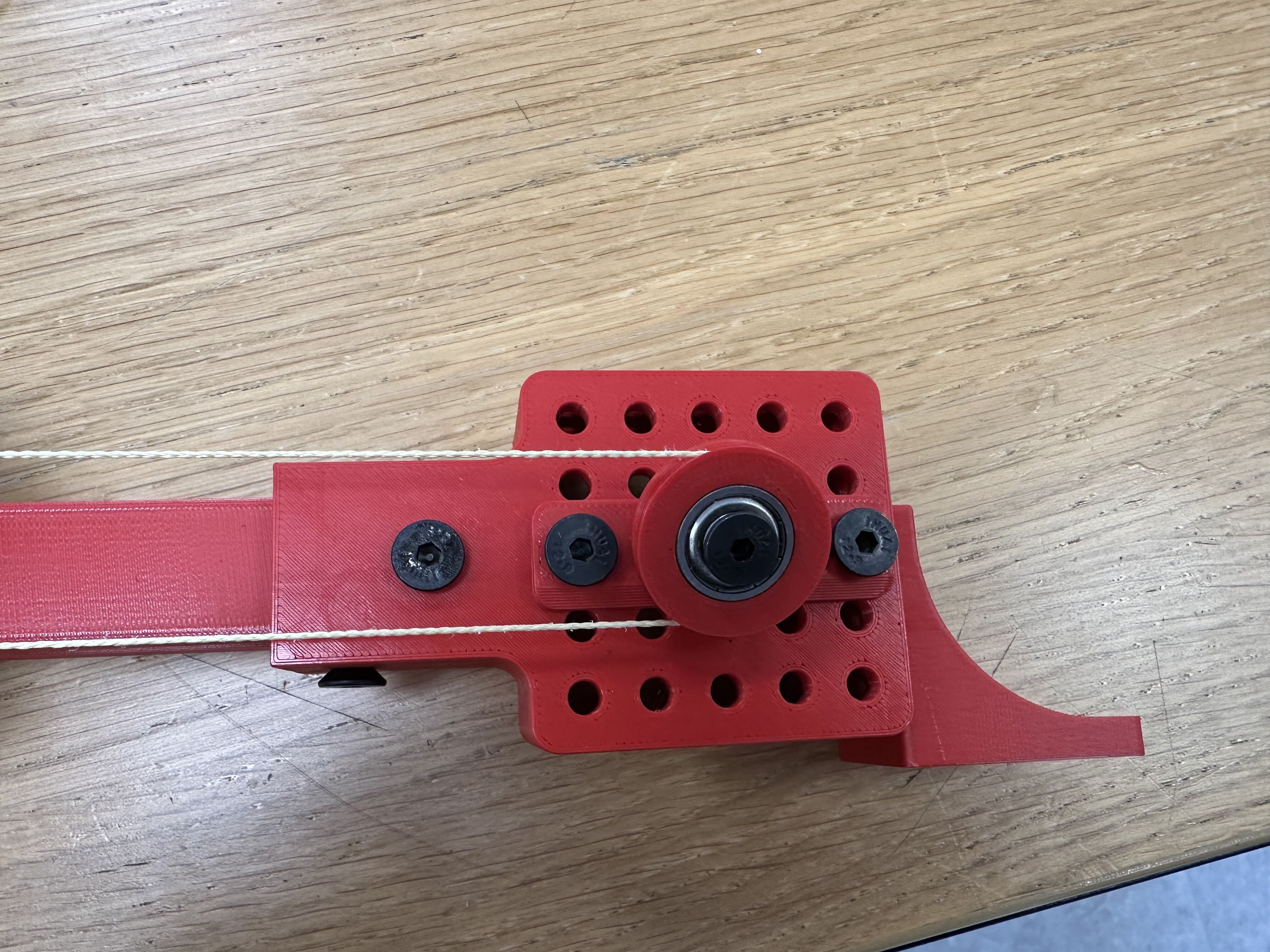
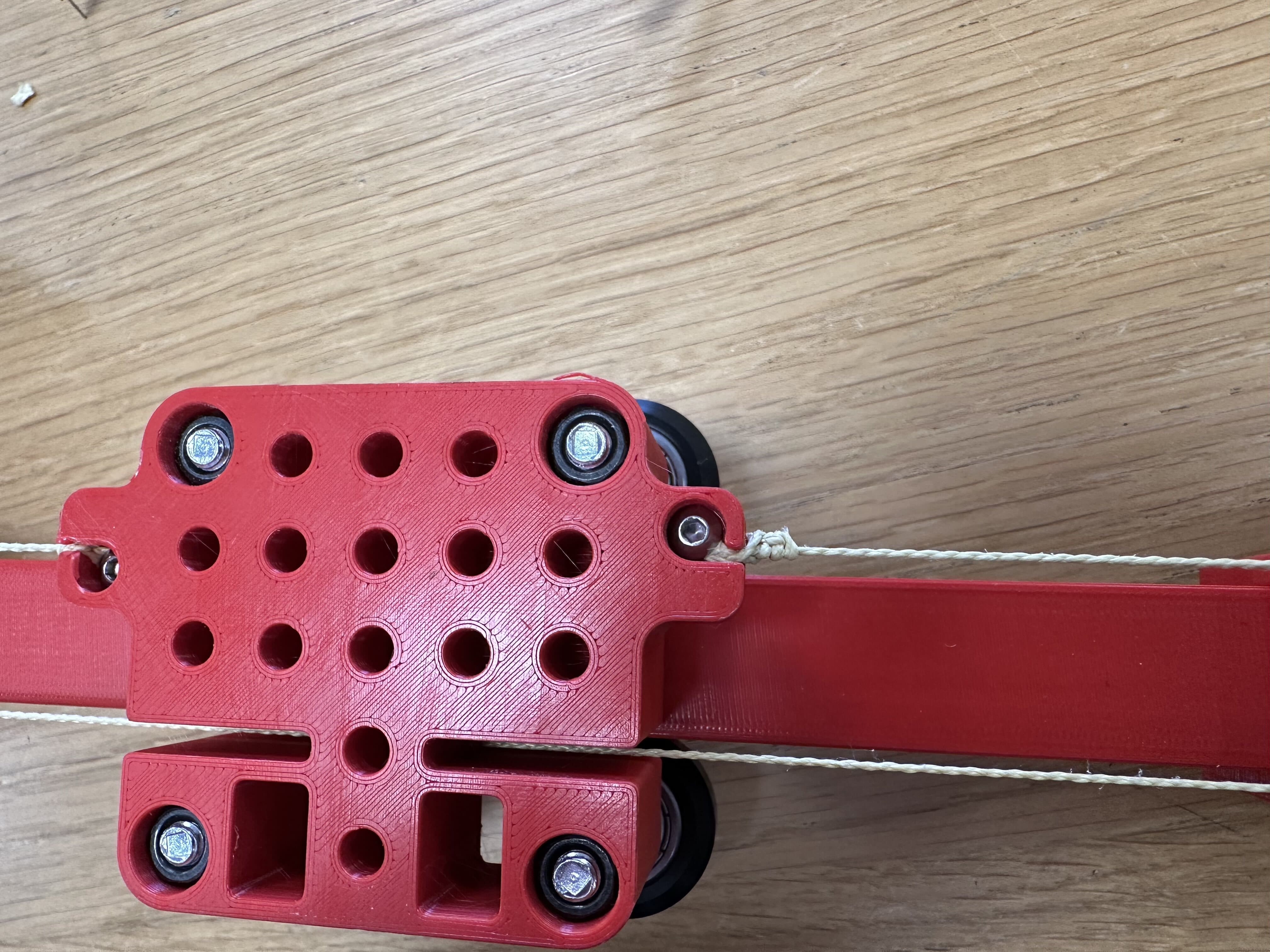
Peristaltic pump
A few different examples of peristaltic pumps were downloaded, 3d printed and tested. The designs were evaluated and new peristaltic pump was modeled in Onshape with parametric design. The pump was printed and tested. The pump was actuated by a stepper motor and a driver board.
Add link to pump file
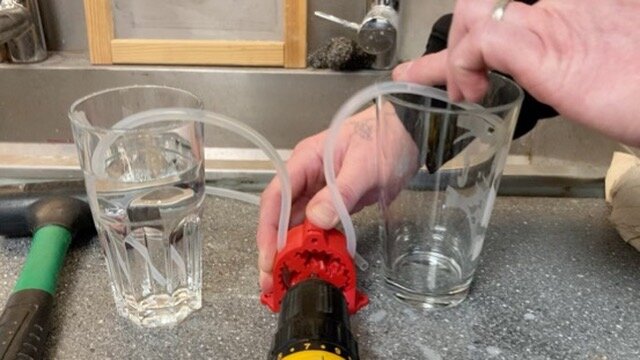
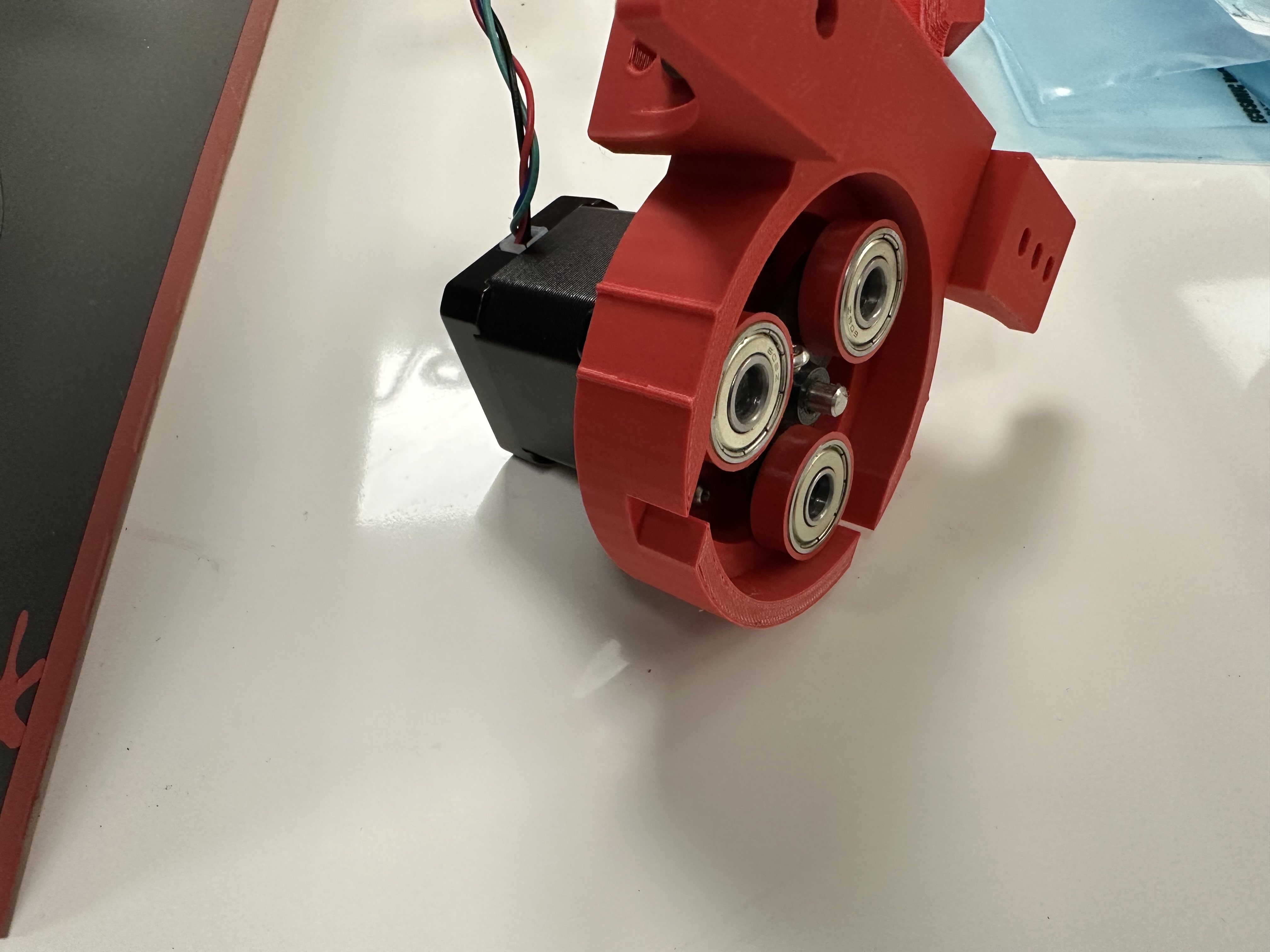
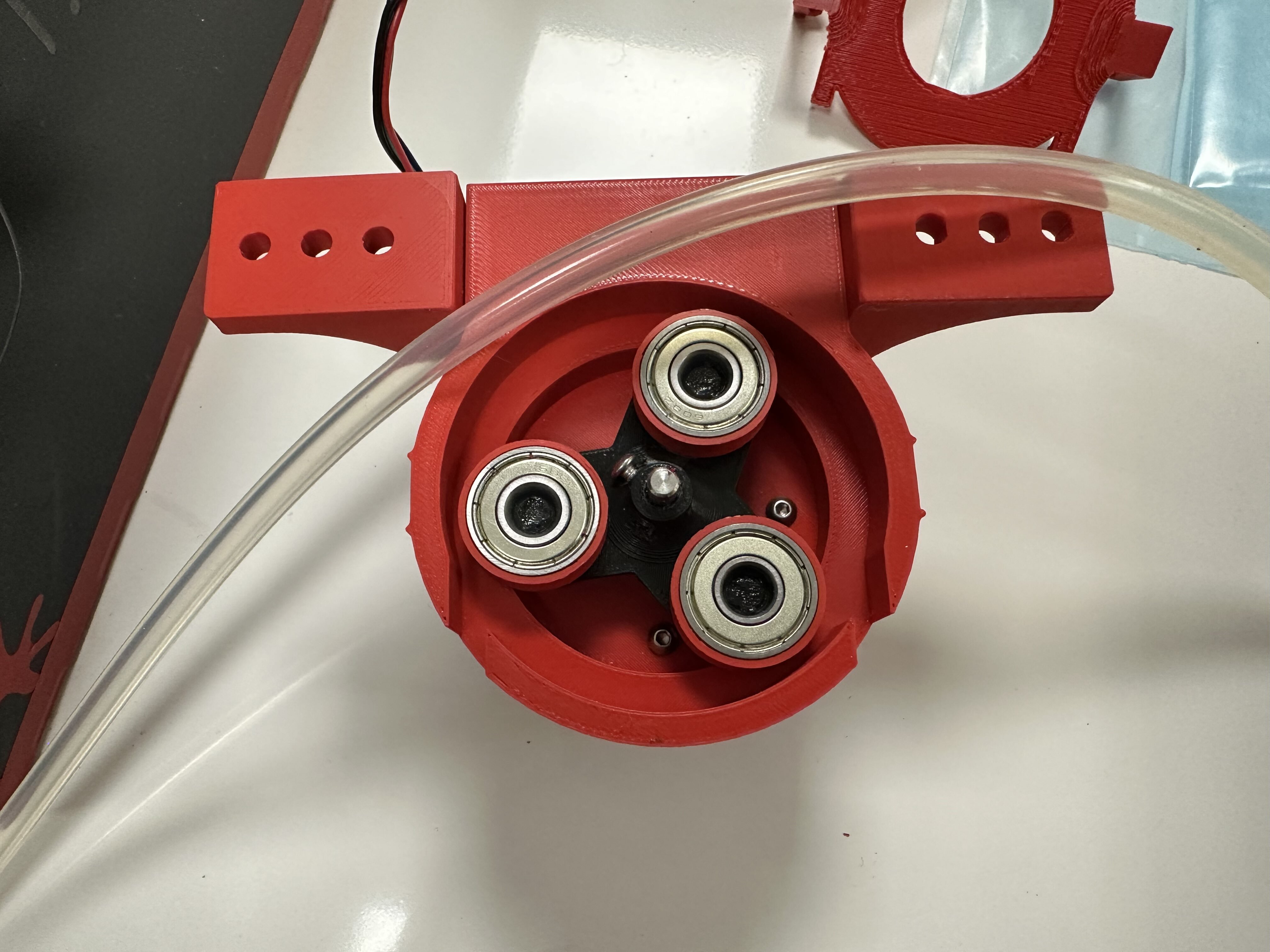
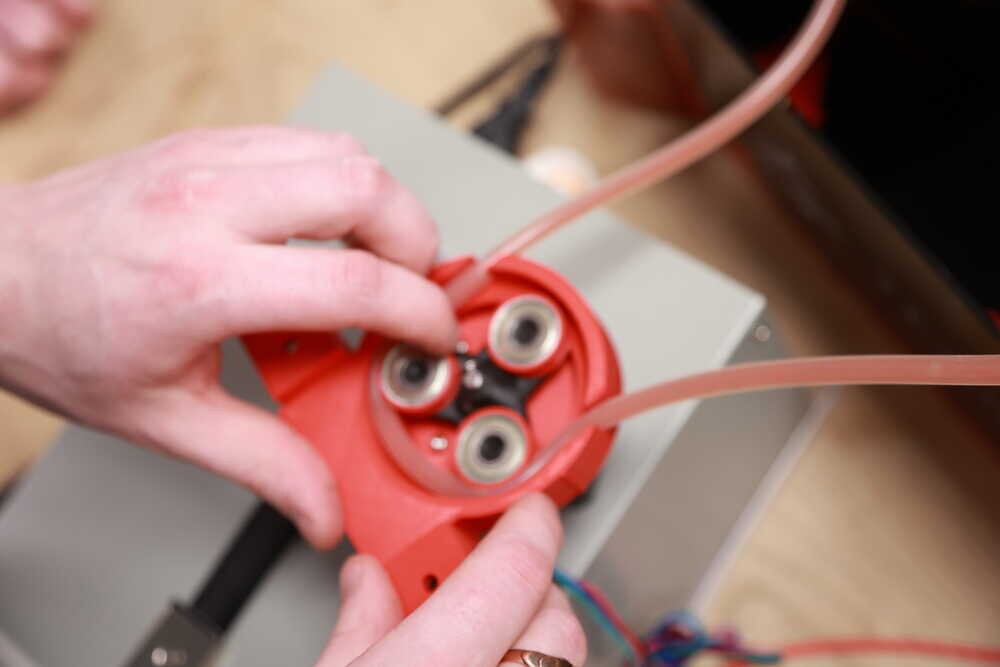
Video showing the axis and pump working
Integration and case
The axis, pump and electronics were integrated in a laser cut plexiglass case. The axis was mounted on the case. The pump and electronics were mounted on the back of the case with controller buttons on the front. The case was designed in Tinkercad and Inkscape.
Add link to case file
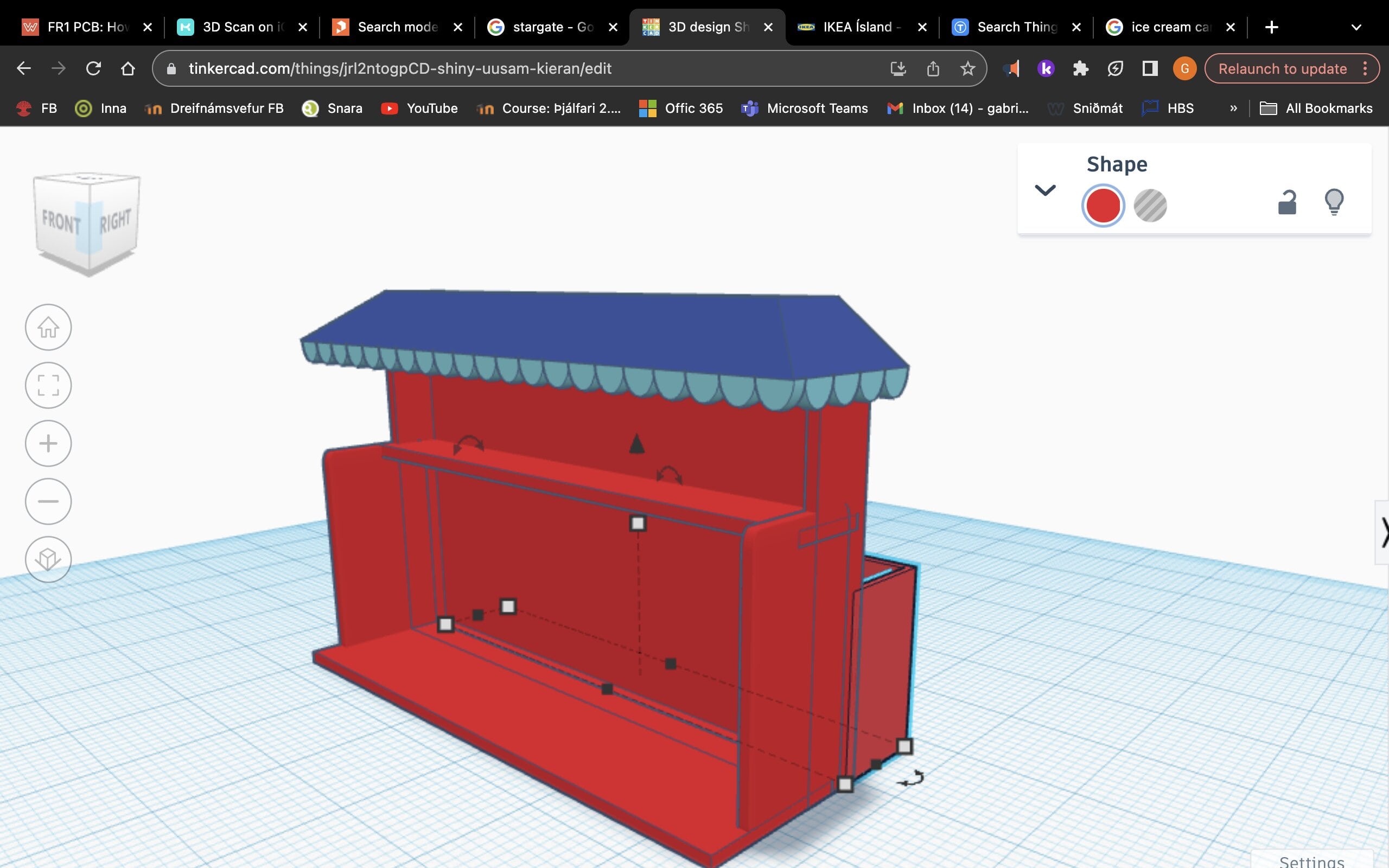
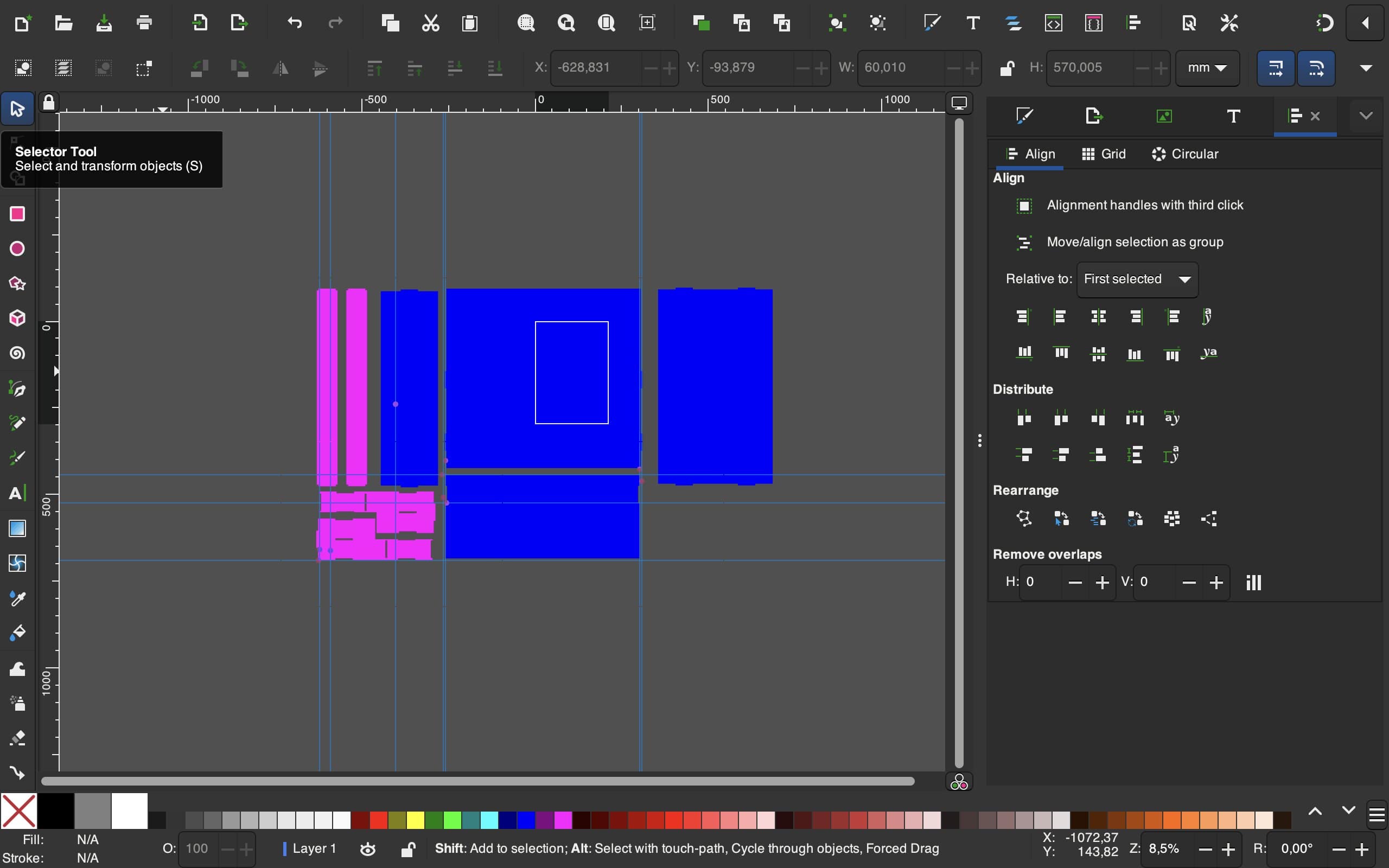
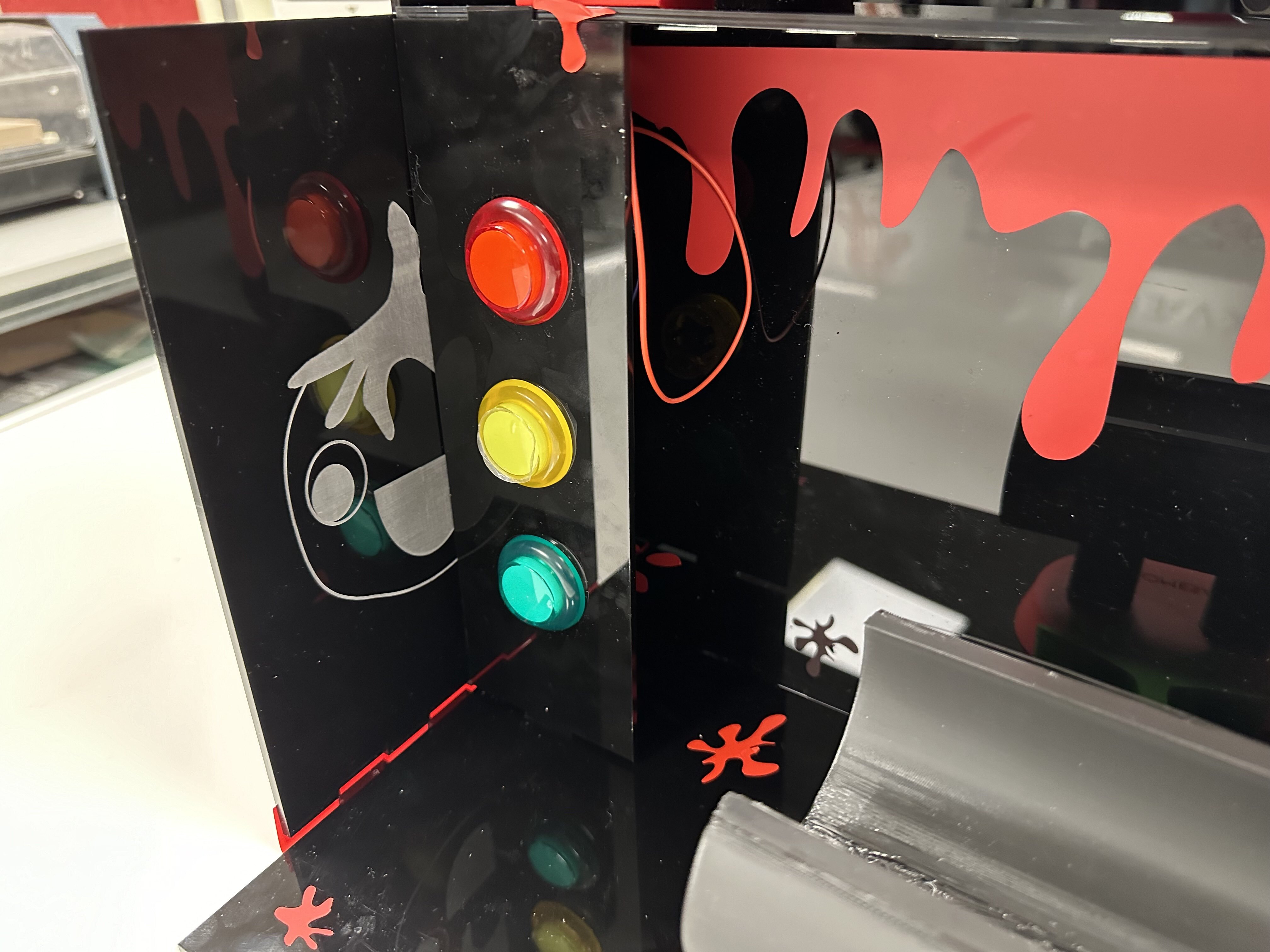

Electronics
We started by using Modular Things by Jake Read to control the machine. We milled the board by Yuichi from the Instuctor bootcamp used to control a CoreXY machine. We used this design because it was shown to work and it had pins dedicated for a stepper motor and a button. Milling and soldering the board went well. We produced three boards, one for each stepper motor.
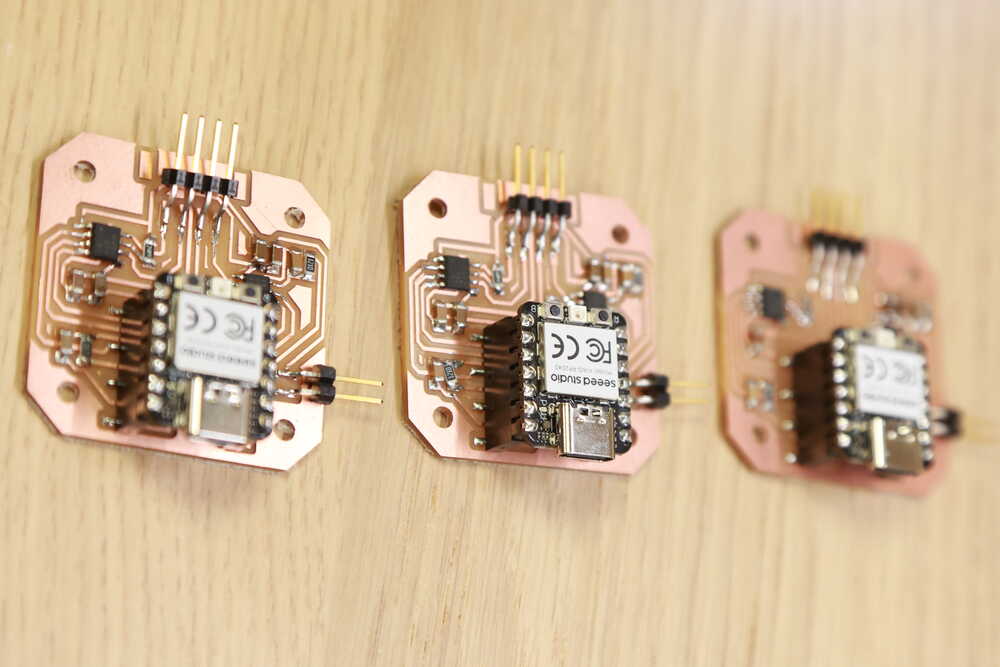
When we tried to control a stepper motor with the Modular Things board we ran into problems. We were able to successfully link the board to the Modular Things Browser controller but were unable to control a motor. We tried different stepper motors but we were unable to get the motor to move. We hooked the board to an oscilloscope and saw that the board was sending signals to the motor but the motor refused to move. We could hear that the motor was making a slight noise and vibrating a little but it was not moving. We spent two days troublshooting the problem but were unable to solve it.
Board on Modular Things and oscilloscope
Since we were unable to solve the problem and had a deadline we had to find another way to control the machine.
Using a Xiao RP2040 and a DRV8825 stepper motor driver we were finally able to control the stepper motor.
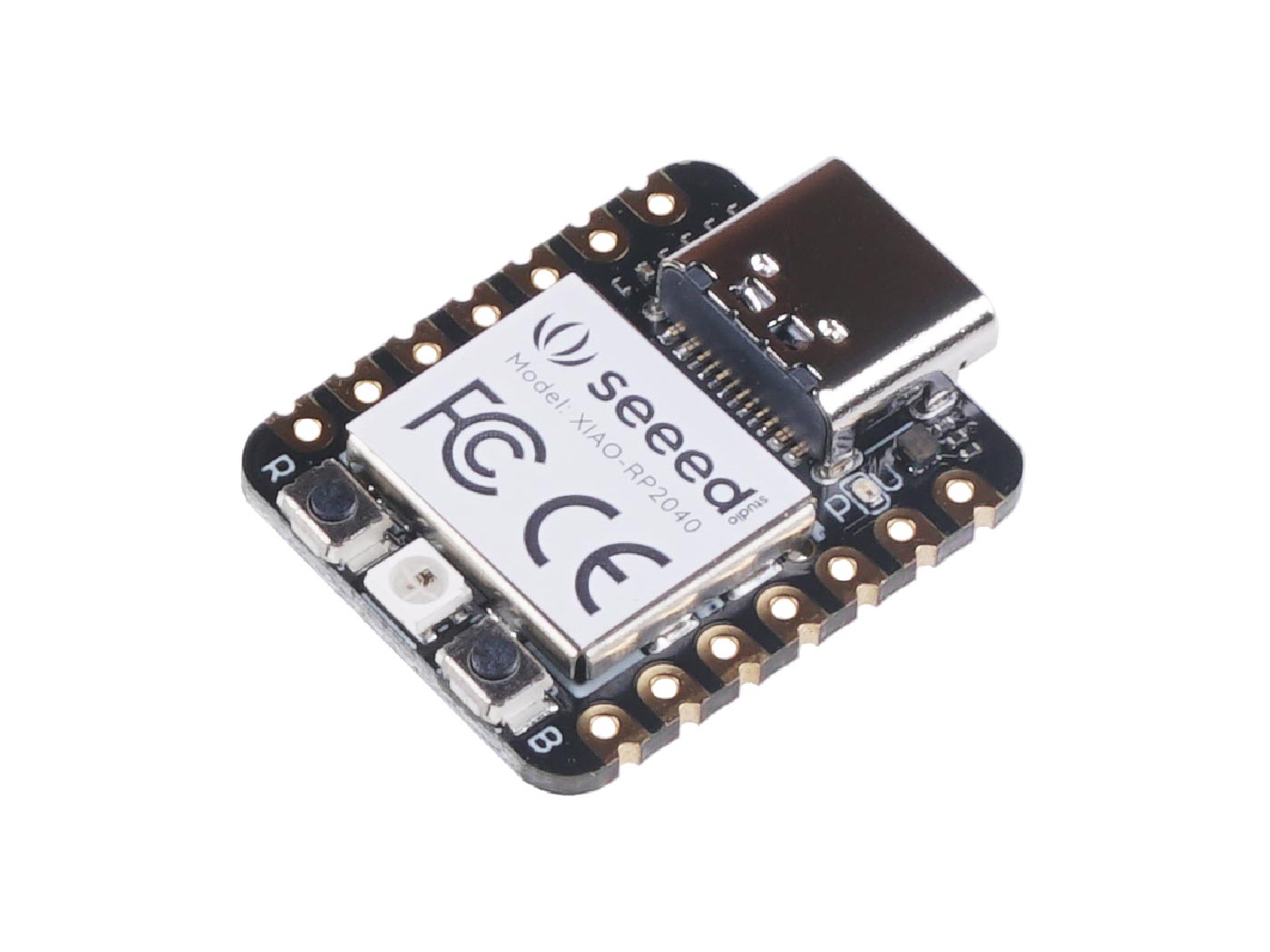
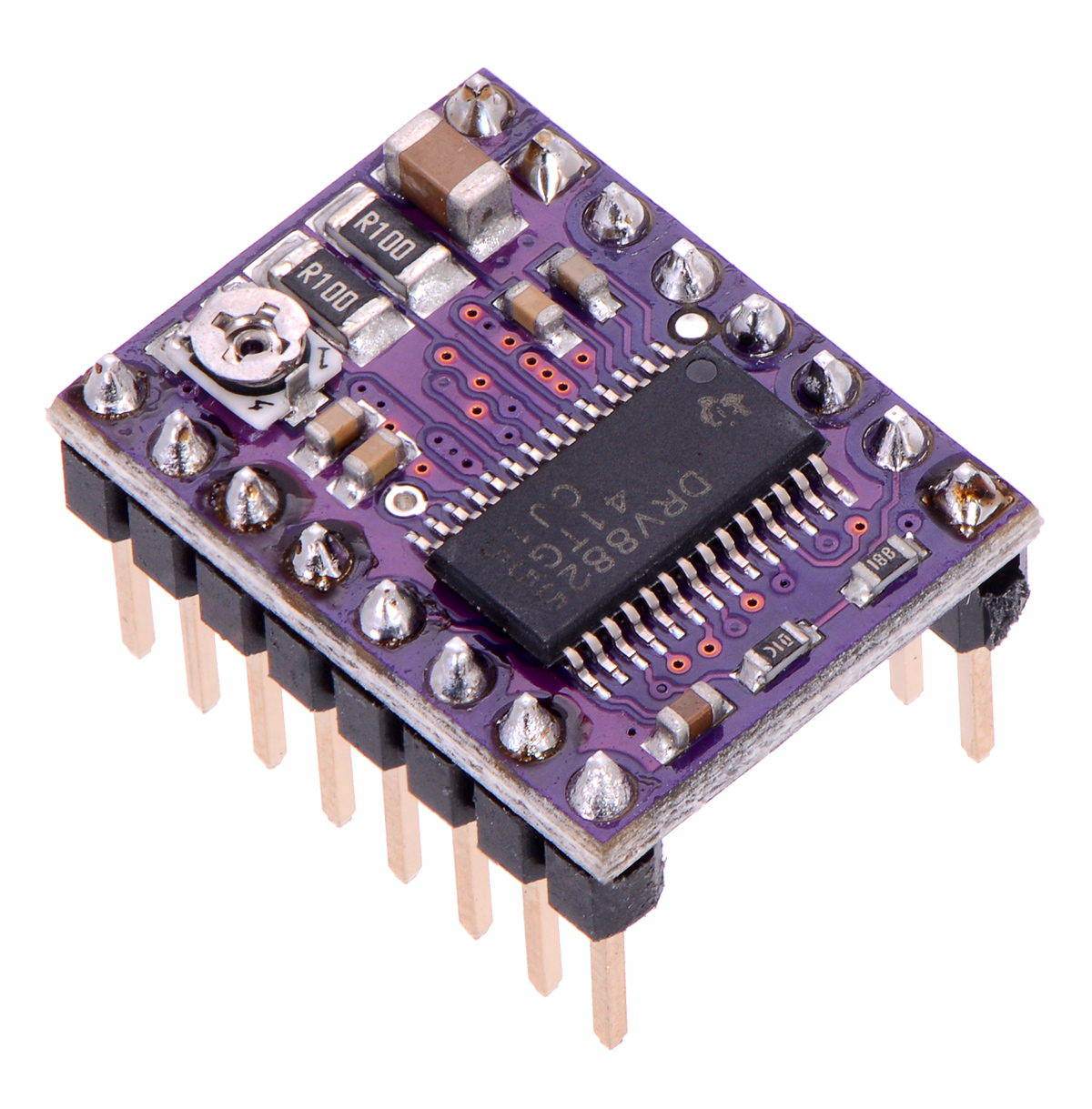
We hooked everything together on a breadboard and used an output power supply test bench to power the motors.
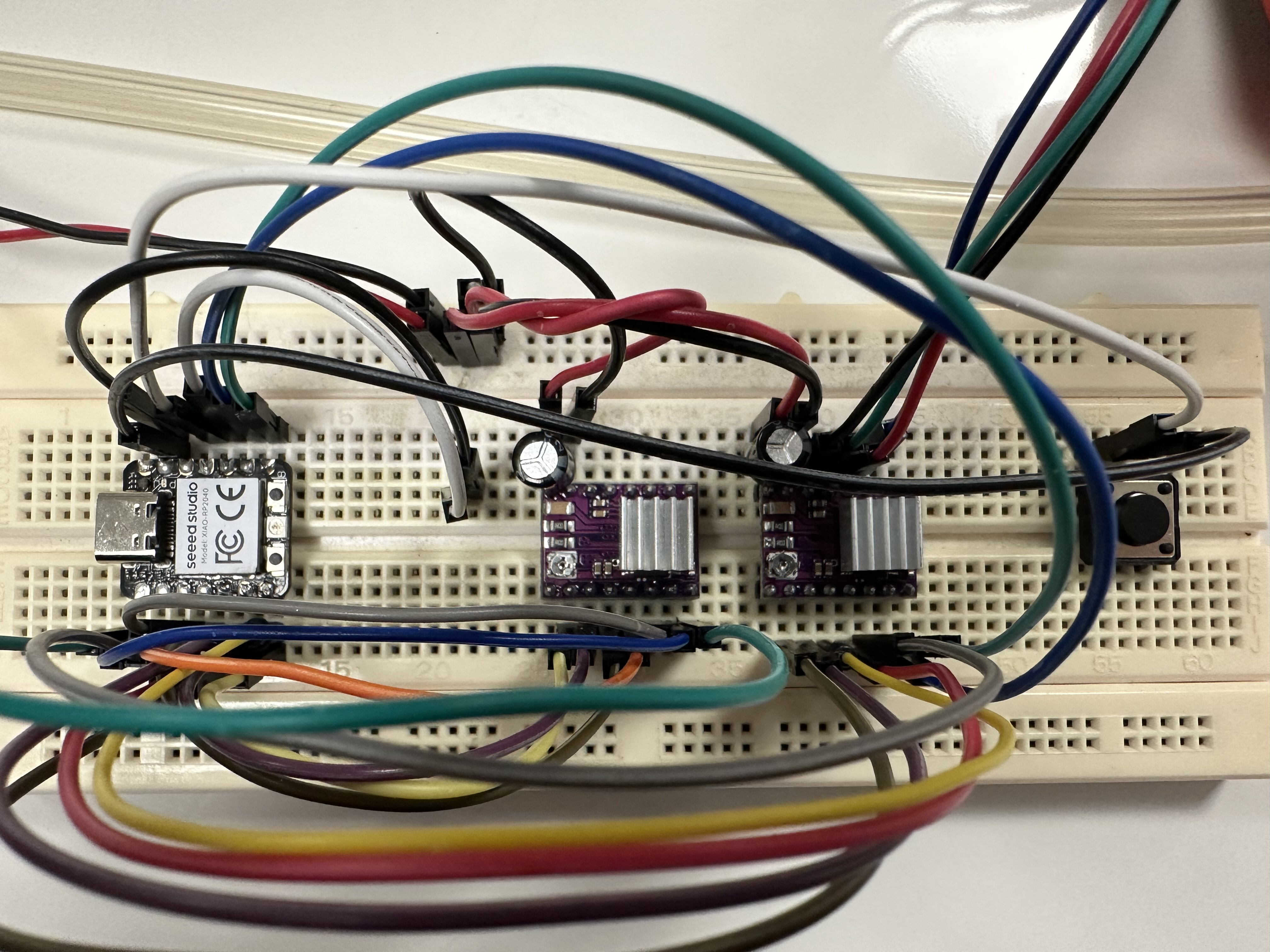
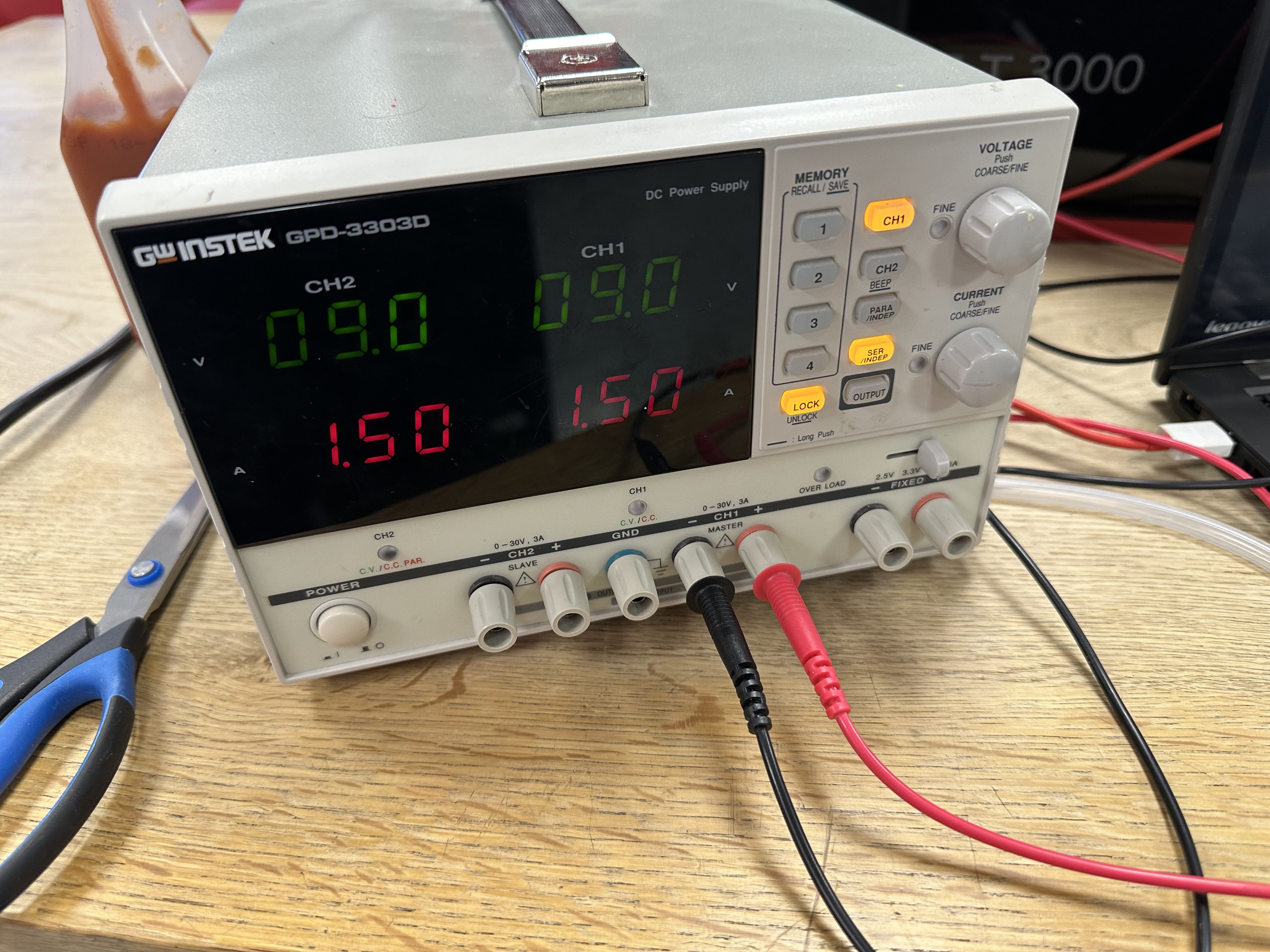
The machine worked completing the first spiral
Code
Here is the code that was used to control the machine
Arduino CodeSpiral 2
As soon as we had the machine working on a breadboard we started working on a more permanent solution. The board was designed in EasyEDA and has two DRV8825 stepper motor drivers, a Xiao RP2040, two buttons and a connection for a 12V power supply.
Future spirals
As of now the newly designed pcb has not been milled. In the coming days the pcb will be milled and tested.
After we have tested the new pcb it will be time for upgrades. We intend to start by adding a new stepper motor to the machine so users can also enjoy mustard on their hotdogs. Then possibly a third stepper motor for remulade.
We would also like to go back to Modular Things and making the machine more modular, making it easier to add or remove condiments.