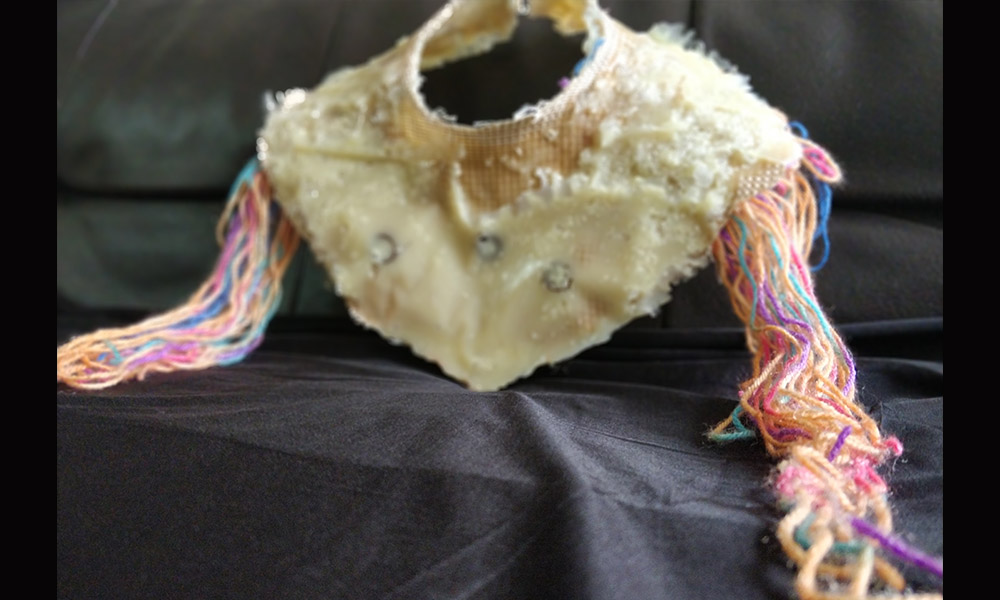
Textile scaffolding have various applications, among which agrotech, building, clothes, geotech, sports, healthcare. This week broadens the perspective of the techniques, processes and applications of technical textiles with references and inspiration of various disciplines. Students are asked to use textiles and fibers to create a textile scaffold or use textile as formwork for their structures
"This week is where having dirty hands has beautiful output"
Nishtha Kaushik
Steps
Step 1: Exploring Textile scaffold
After seeing amazing pieces of art and form work in week's lecture, this week seems very interesting.
The one below worked where I used Denim piece with Alum, where i boiled alum andpoured it in a can and hanged denim with a string and left it for 2 nights.Therefore, I decided to start with preparing my mold by 3d printing and forming a Neckpiece collar for myself and another technique ill be using would be Crystallisation. Initially I did some crystal tests to explore which fabric works and what doesnt ,here I used alum for growing crystals and left it for 2 nights on 2 different materials.
Below Image is the failed one where I used Boric Acid which I thought is same as Borax and was very difficult to find here. It didnt work at all, no crystals formed ,only foam.
Step 2: Mold Making "Under the skin" Neck Piece
I started by taking my scan file from Mahavir and then my neck from it and imported it to meshmixer. I call this "Under the Skin" concept where I plan to design a Neck Piece with design of Organic nerves which we have under our skin actually being visibleabove the skin. Iwill play with Meshmixer to dothe same. Worked on it a bit and then made it STL file and 3D printed it. Only thing I wasnt happy about was wastage of material due to heavy support required.
Below I have my 3D scan file opened in 3D builder, I plan to use thisfile for my this week, its my 3D scan taken by Mahavir in Digital bodies.Below I used plane cut option in 3D builder to remove part which I dont need. This option maks thepiece sable and flat on ground, whch is very useful if one planning to do 3D printing.
I Import this Stl to Meshmixer which basically helps in making this piece organic and for sculpting,I really enjoy using this software, it helps forget the dimensions of a design and justplay with it understanding principles behind it.
In the picture below, I thought it will be easier to cut negative from cuboid to have a nice piece easyto3D print. So below is the image used for taking negative out from the cuboid.But I boycotted this method and went on working directly on my STL file.
Below are the processes used on Meshmixer for my neck Piece. The purpose behind making this Piece was to see if this can work well with my Final Project.
Below is the final piece made on Meshmixer.
E-Neck by nishtha on Sketchfab
Step 3: Textile Scaffolding
While 3D printing,
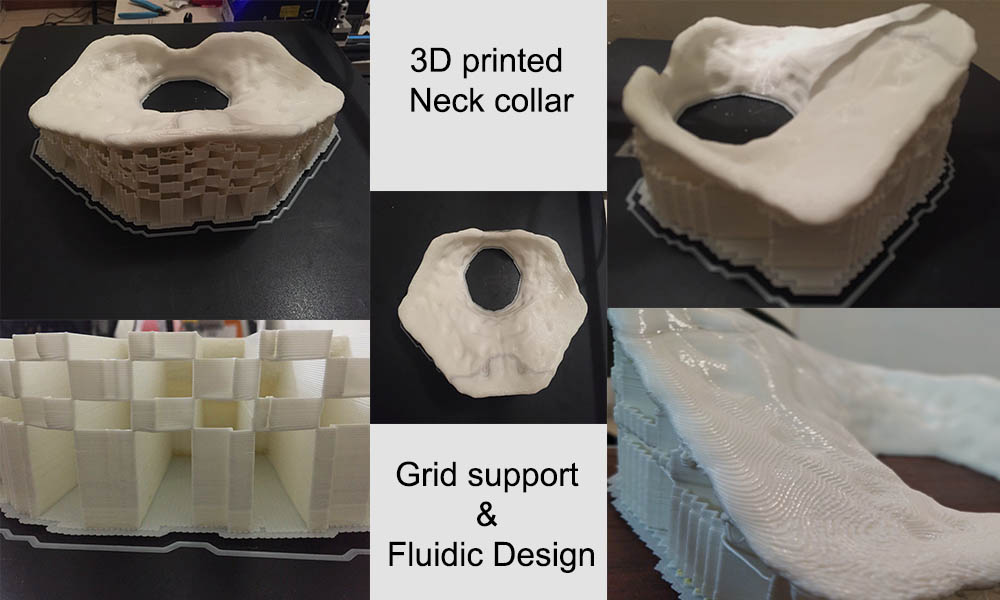
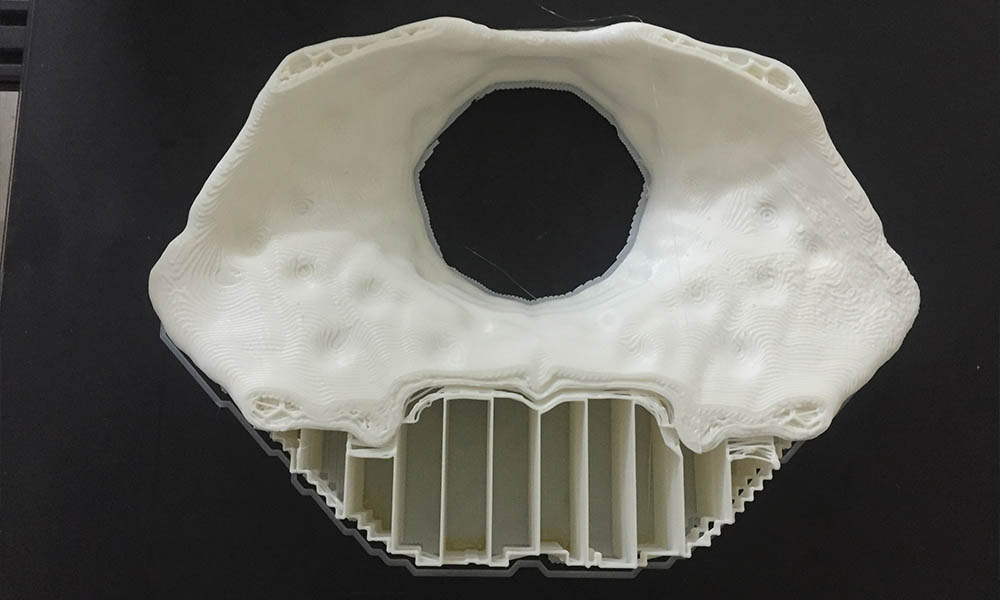
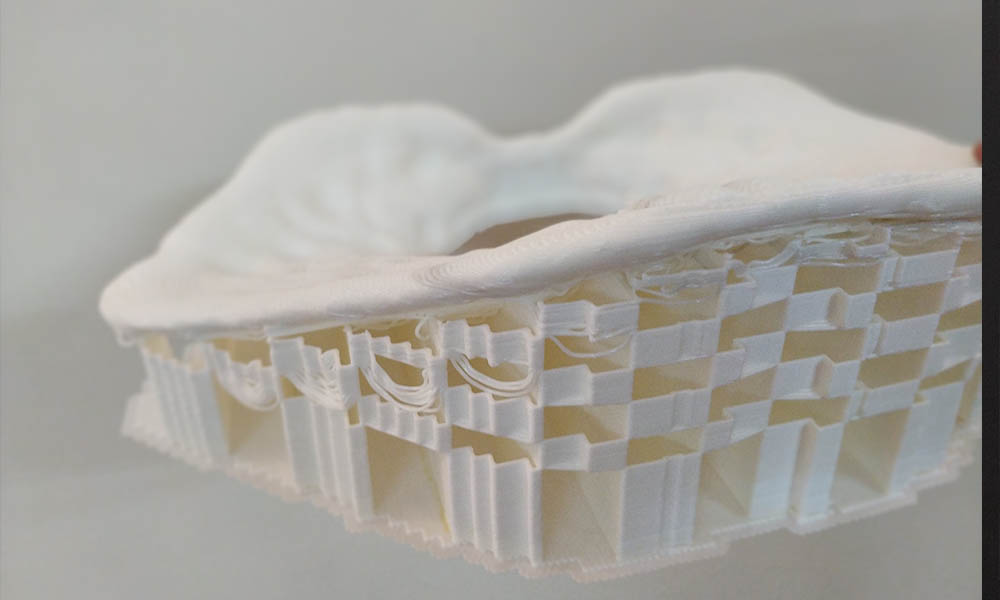
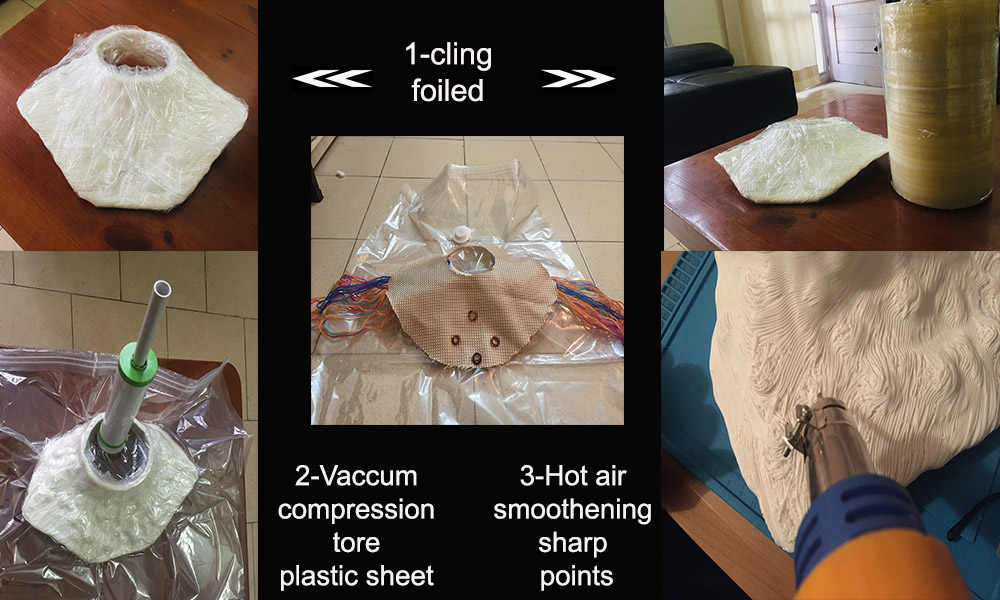
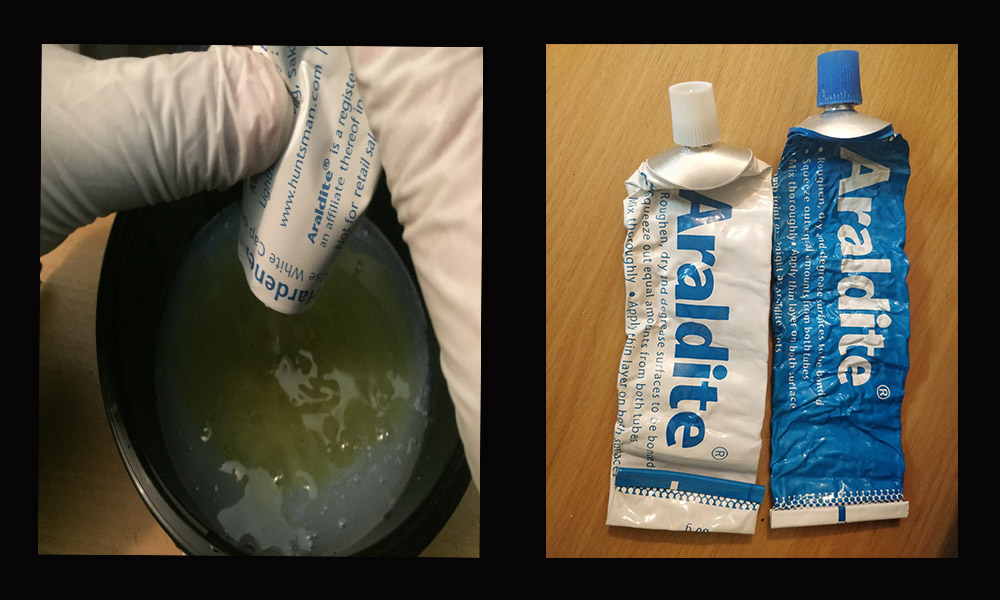
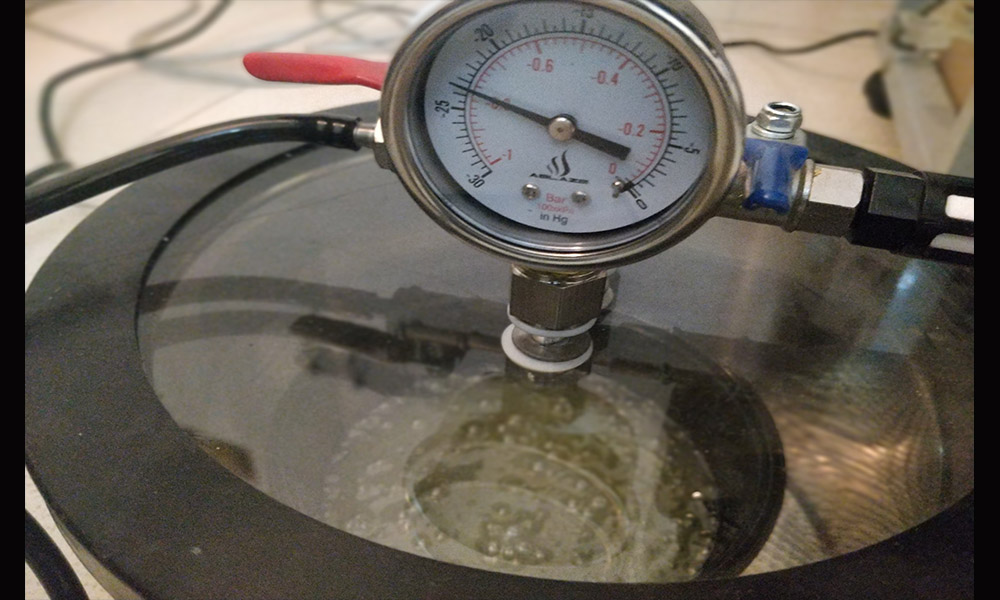
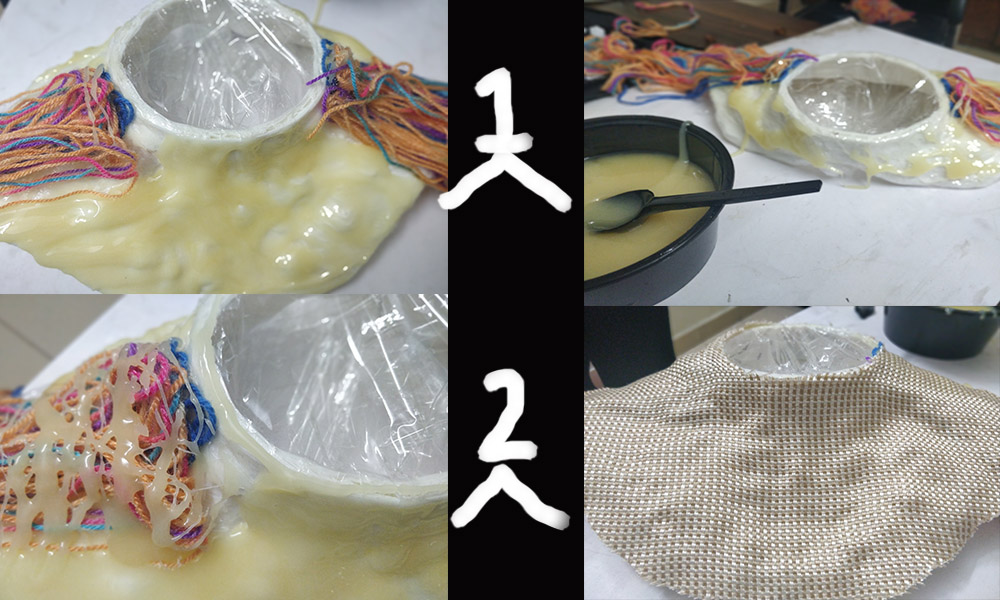
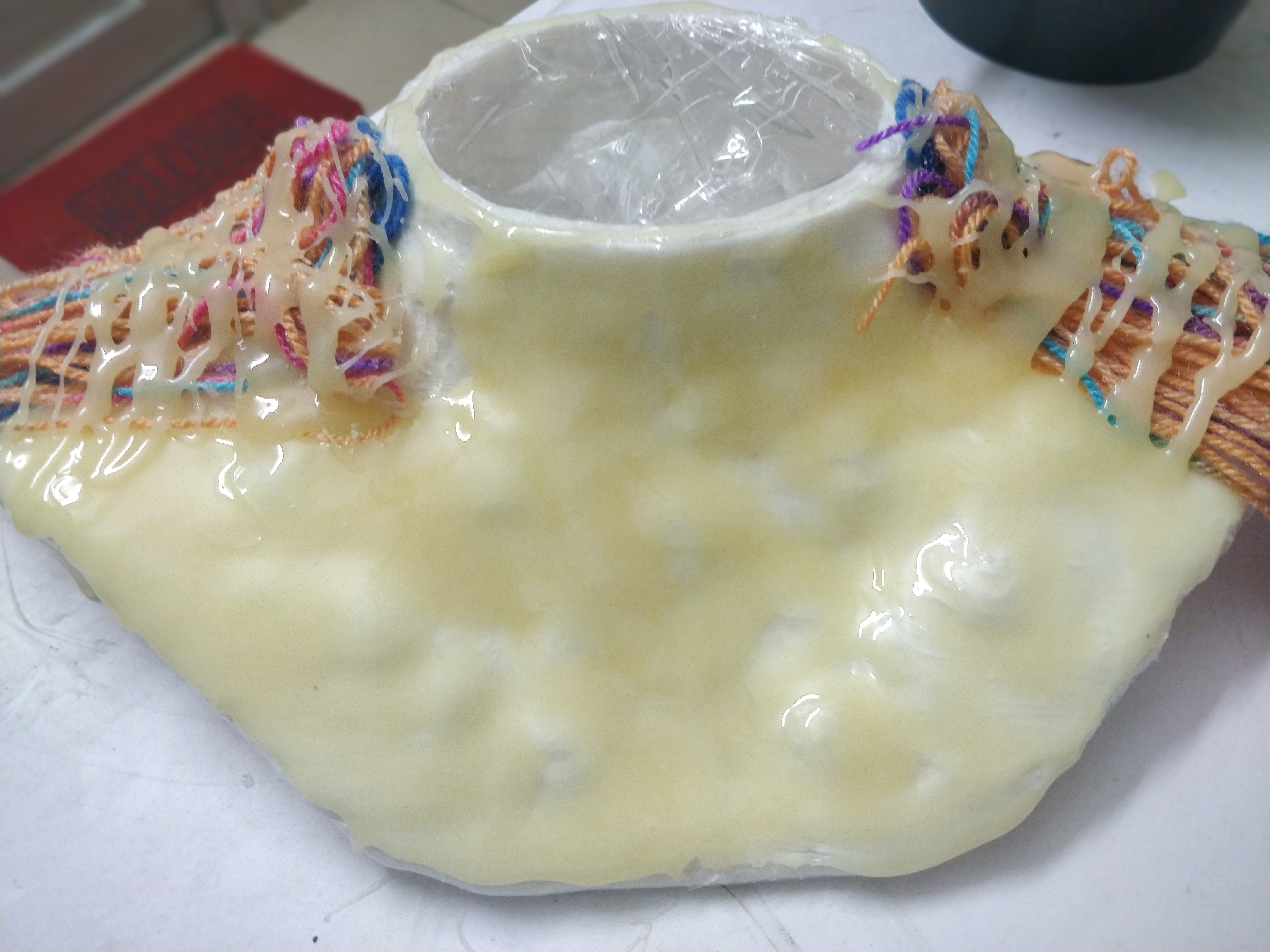
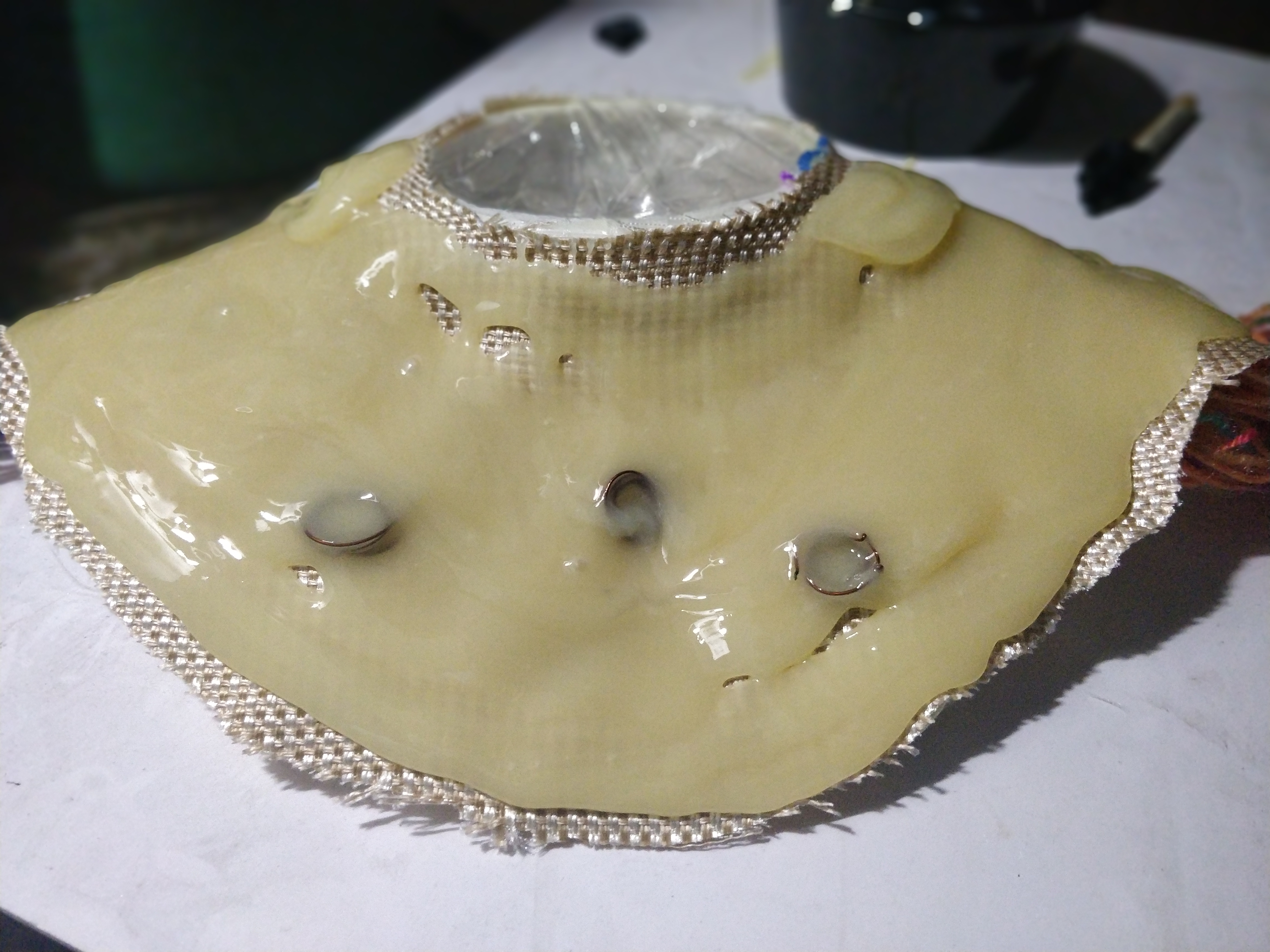
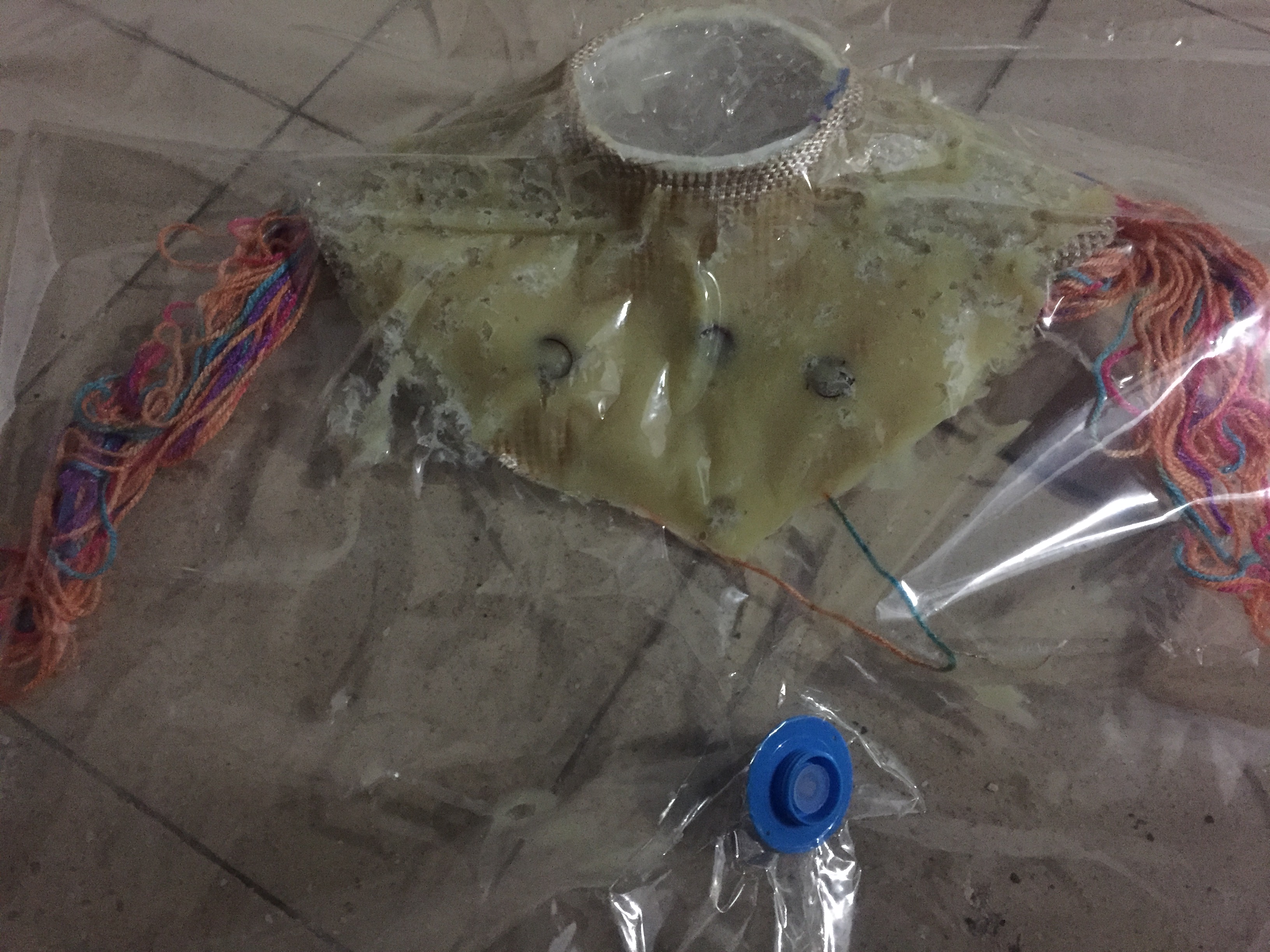
Below At one point I felt that I should keep this part of the support for sesethics but its doesnt fit well on neck if same is kept.
Below is an image of the grid support for holding the piece on areas it has either non flat base of is at a height.
I started by wrapping it with cling plastic foil as my base for composite and then
PROBLEMI Vaccum bagged it but as my piece had some sharp points so vaccum bag got punctured and it didnt work. Then SOLUTION I took Hot Air blower to melt the sharp points and made them smooth and decided to use the same for compressing my cling foil and a way that it takes shape of my design. Below are the images while its 3D printing with support. Thats a huge support.
Then I used Araldite epoxy resin which had 2 tubes in one packet one is Hardners and other is resin. They are mixed in equal amounts. I used almost 500gms of Resin and 500 of hardner, But last time i tried composites Ifaced a chalenge where I mixed hardner and resin and then used Vaccum chamber to remove bubbles but it also ended up becming hard to spread, so this time i poured Resin , vaccumed it and then poured hardner which eventually didnt had bubbles as well as wasnt hard or cured.
Then First stage of cling foil,
Second was to spread One layer of Epoxy Araldite Resin , then I spread my woolen threads and poured another layer.
Third step was to place my Piece of Cloth which was Jute Hessian cloth and few spiral pieces of Copper wire as i want to use this neck piece as my Neck Mask for Skin electronics if it comes out well.
In the picture below, it clearly shows the organic design very well and gives a feel of SKIN or under the skin. I so wanted to leave it right here but Ihd to proceed further with anothr layer of Resin.
In the image below, I poured another layer of resin, I first tried to be constant in terms of flow of resin over the piece but It was difficult to do so after vaccuming the resin. But then an idea struck me topour diferent thicknesses an enjoy the beauty by probably installing LED below it.
Fourth Step was to Pour a thick layer of Resin and few crystals over it and in the end i vaccum bagged the whole piece.
Step 4: Output
First OutputFinal outcome came out beautiful except the last layer of resin was so thick that the crystals submerged.
In below Image , it looks hard but it was very soft from inside. I even cut it from the back so thats it easy to wear.
The UNDER THE SKIN : NERVE
The image below have embedded Neopixel strip for showing the different thickness of resin
After few trials
Step1: Plastic base
Wrapping my piece with plastic sheet as a Release fabricsand then I covered with the breathable fabric
Preparing the epoxy resin.
This time I am using resin which has high strength but medium Viscosity with the Ratio 2:1 where 2is resin and 1 is hardner. I painted resin over the breathable fabric and then my fabric which I want to scaffold into a shape.
Vaccum bagging the my piece to distribute resin throughtout the piece and so that its ableto spread.
Final outcome:
Step 5: Crystallisation
Using Felt material and alum I made these cufflings andialso used my Computatinal Couture piece and crstallised it to give it a shape and harden it so that it fixes its shape. Pictures explains :)
I crystallised my piece back from computational couture but it got very hard and I realised that the shape Lycra took became opposite to what it was after crystalisation. Learning : One need to be careful at what angle, position you are keeping your Piece for crystalisation in the Alum Water.