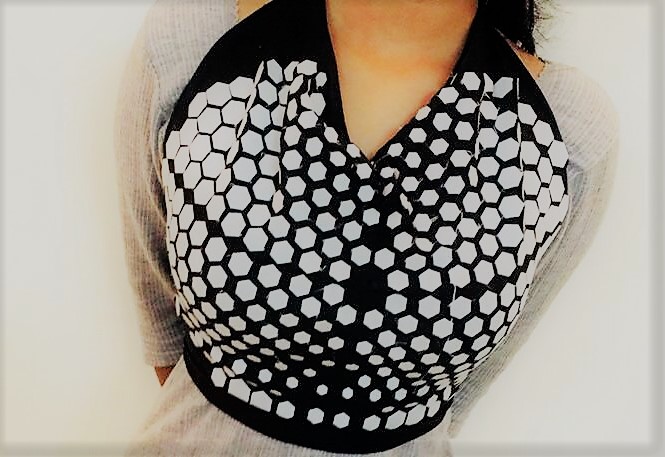
This week has been about learning Rhino and Grasshopper. Grasshopper really interests me to do maths to derive design rather vice versa. I personally would take my learning curve towards blender because i have been planning since long to explore that software. But for now Rhino asks for lot of time and practice to be able to use it efficiently. I have my previous experience with Firefly Plugin in Rhino of a basic level.
Deriving Design from data is an interesting concept specially if you are looking for organic Design. So after Rhino , try Blender
Nishtha Kaushik
Steps
1. Exploring some interesting Design elements and Installing Plugins
started by exploring different computational designs.
As much exciting it is to update your software, I would recommend to use Rhino 5 as it supports most of the plugins unlike Rhino 6. To avoid such risks, i am sticking to Rhino 5. You can download its 1 day trial for use too.
One of the best examples IRIS VAN HERPEN, this really blows my mind, and I eallylook forward to gain some experience on this concept. This shows how computational desiging has been given life in to a fabric
Similarly, this one brings focus to the concept of stretched Fabric bringing 2D into 3D shapes.
Coming to what I plan to pursue this week, starting with this:
2. Following up tutorials and my Design
After a really helpful lecture by Aldo and Eugenio. I started following the learning process, to explore as many components possible. I wanted to go slow so that my basics are clear with this. I totally agree its an addiction so started working on two things Hexagons and attractor points for this week.
I started making my file from the tutorials taught by eugenio but made minor changes to learn more. In the image below,i chose Hexagrid to start with. Selected Number slider to give dimensions for X-Y-Z.
I Moved on to using Remap, curve, Extrude and make atrraction points to control the movement of my hexagons. i have attached my Grasshopper file for the script. As I planned to print 2D on lycra and deform it into 3D. This works well for me.
Then ou can see all the views fromTop,Right, Perspective how the design looks, majorly my focus was on side view and i prefer working in Perspective view.
Saving both the files with same name: both means Rhino as well as Grasshopper.Saving it in stl format. Though you will always find grasshopper files (script) in grasshoper itself when you open the software.
3 Design to G code
After Designing, I exported in STL and opened it in Simplify 3D and did following settings.
In the above video, one can see I chose Nozzle diameter as 0.8 as I installed new nozzle of bigger size since smaller ones would not adhere to non levable fabric mid print. Secondly extrusion multipler,the extrusion multiplier will multiply the amount of filament extruded for your entire print. This includes skirts, rafts, supports, perimeter and infill extrudes. The default values in the software are .90 for PLA and 1.0 for ABS. I kept 0.89 as I would be skipping a layer when we put in the fabric mid print and so it needs to ooze out only plastic enought to compensate for my 4 layer print.
Thirdly, retraciton is how much filament will be retracted when the software does a retract. Mine is 10 mm because my bigger nozzle and flow rate needs to be controlled so as not not ooze plastic all over your fabric when nozzle jumps between my islands.
Fourthly, top and bottom solid layers are 3 each as it gives me enough adhesion at base and at top my hexagons get covered properly. It represents number of infill layers that will be placed at the top and bottom of your part.
Fifthly, Outline perimeter shell is 1 only as this is a bigger nozzle which is equivalent to four such outlines of a 0.2 nozzle. Outline shells will trace the outline of your part, and extrude at your extrusion thickness. The printer will print the outline shells, then print Infill afterwards.
Sixthly, first layer height, this % will take a % of your Primary Layer Height. Mine is 85% to compensate for my bed level which I cannot manually know which is enough- This is via trial and error over multiple job works the fablab has done-it keeps changing everytime we relevel the bed.
Seventhly, Bed temperatue is 60 degree as when I printed in winters where environment temperature was 12 degree. inspite PLA not requiring bed level, it is needed in winters at least to avoid warping.
Lastly, Bridge setting-default-no need to change as my design has no bridges needed. Same goes for other settings in advance-my print doesnt need those to be tweaked as there are no thin walls but all are solids without any cantilivers or fine features smaller than the nozzle size so all those settings I ignored.
4 3D printing
After setting up in Simplify3d, I created Gcode, uploaded on our 3D printer, starting by heating up the bed to 70 degree celcius, and then i slowed down the flow so that it goes slow for first 2 layers without failed retraction.
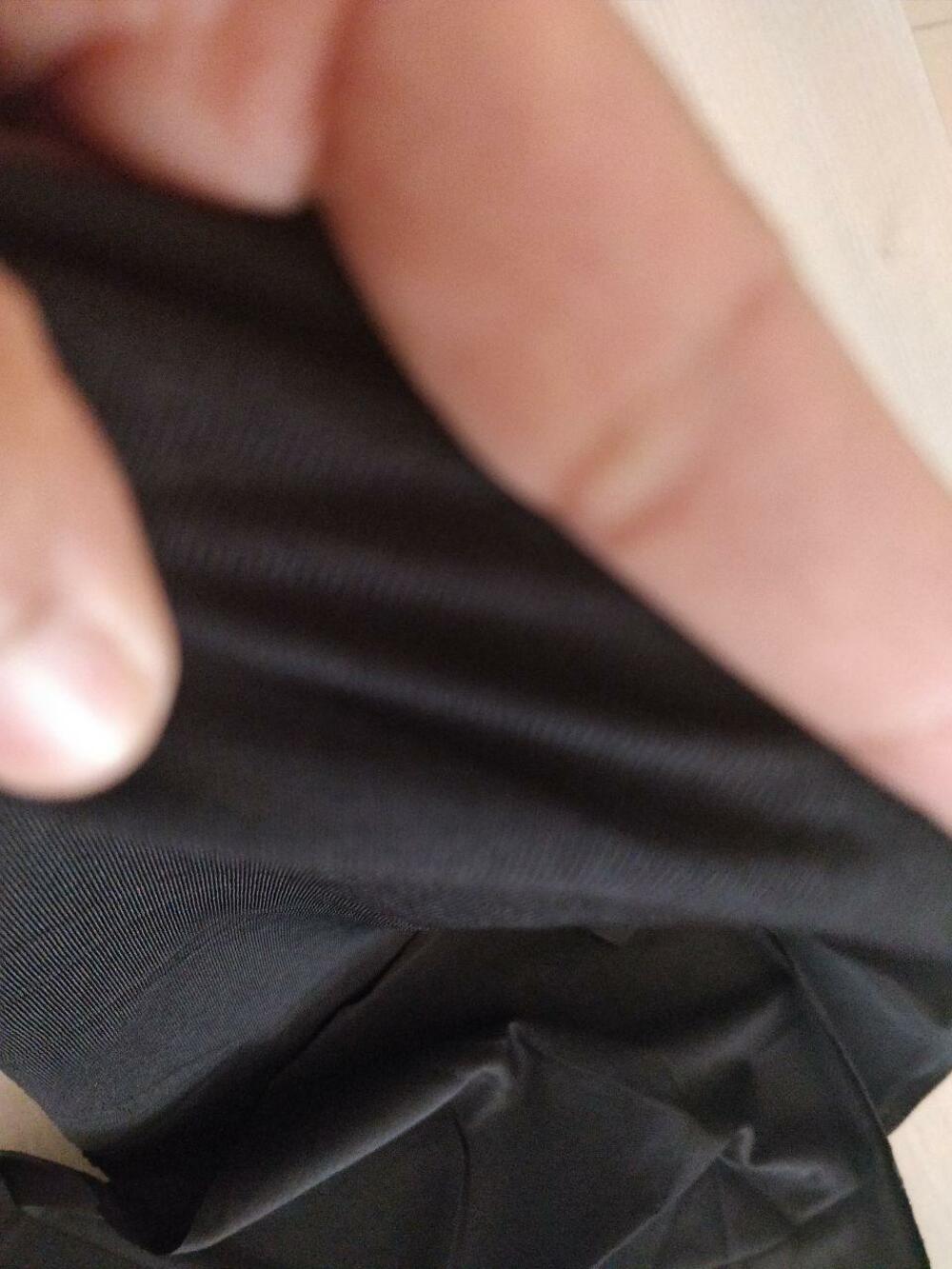
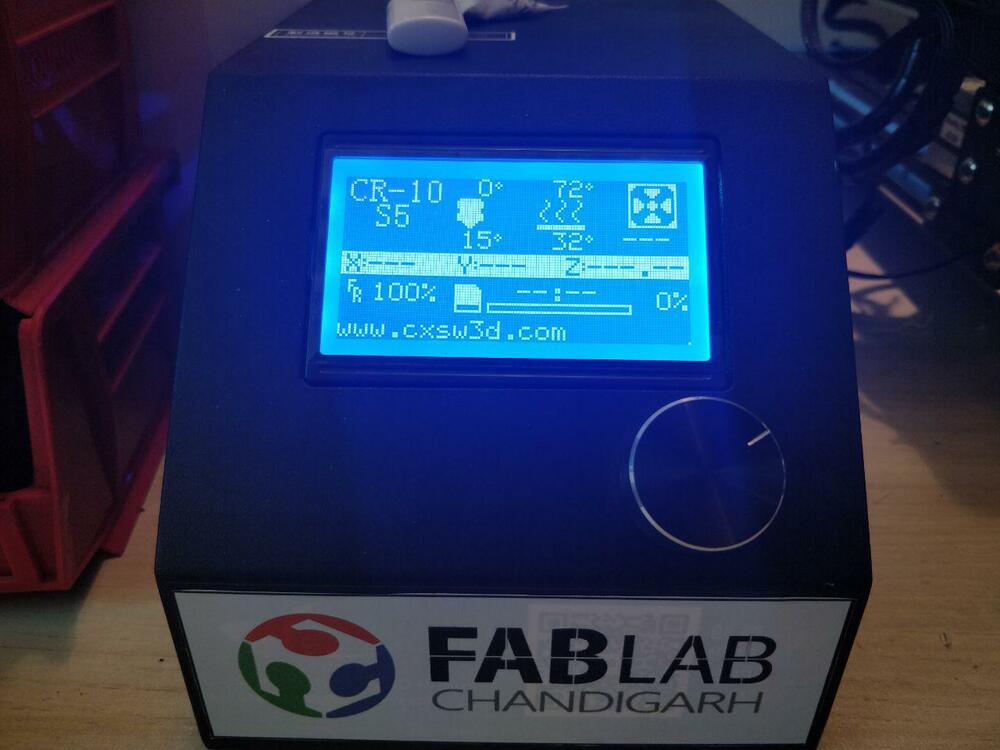
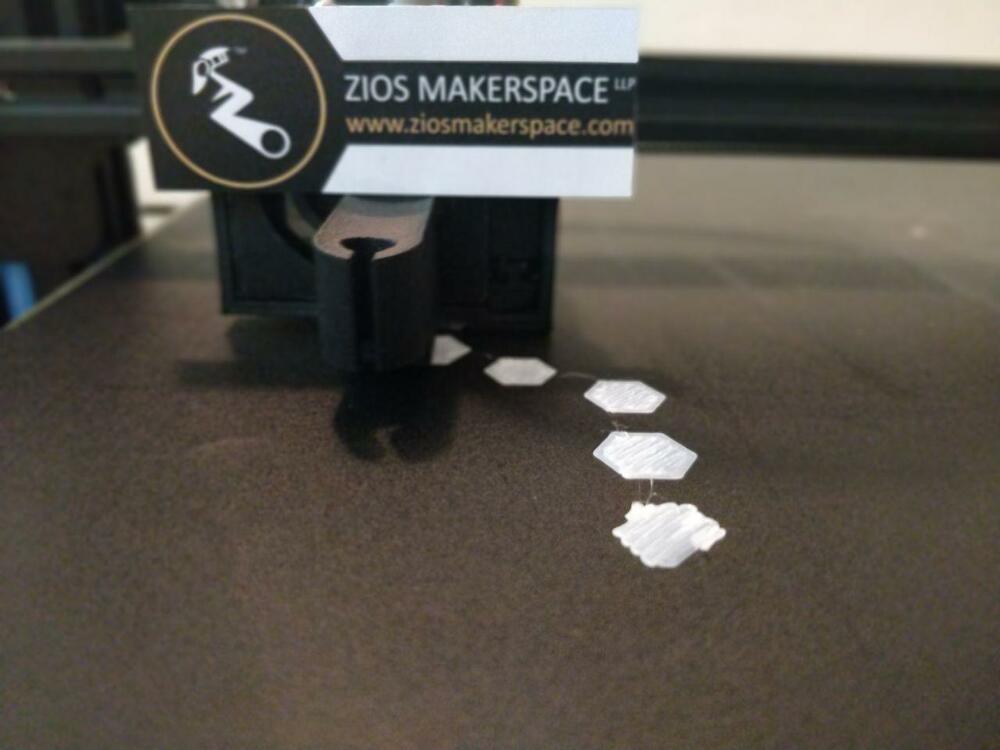
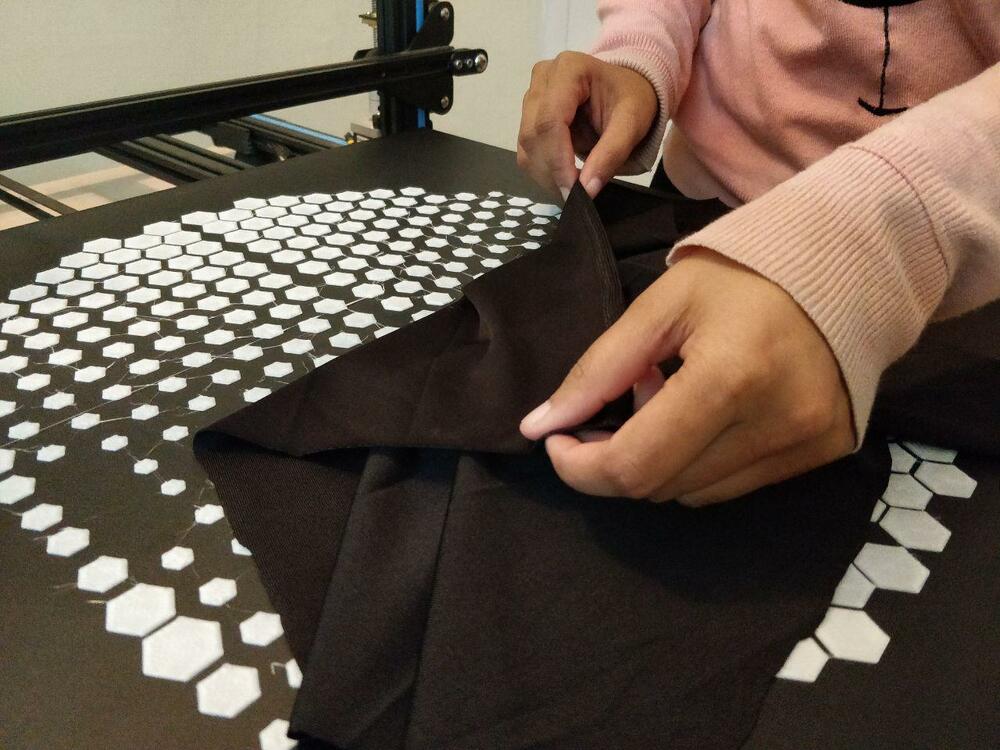
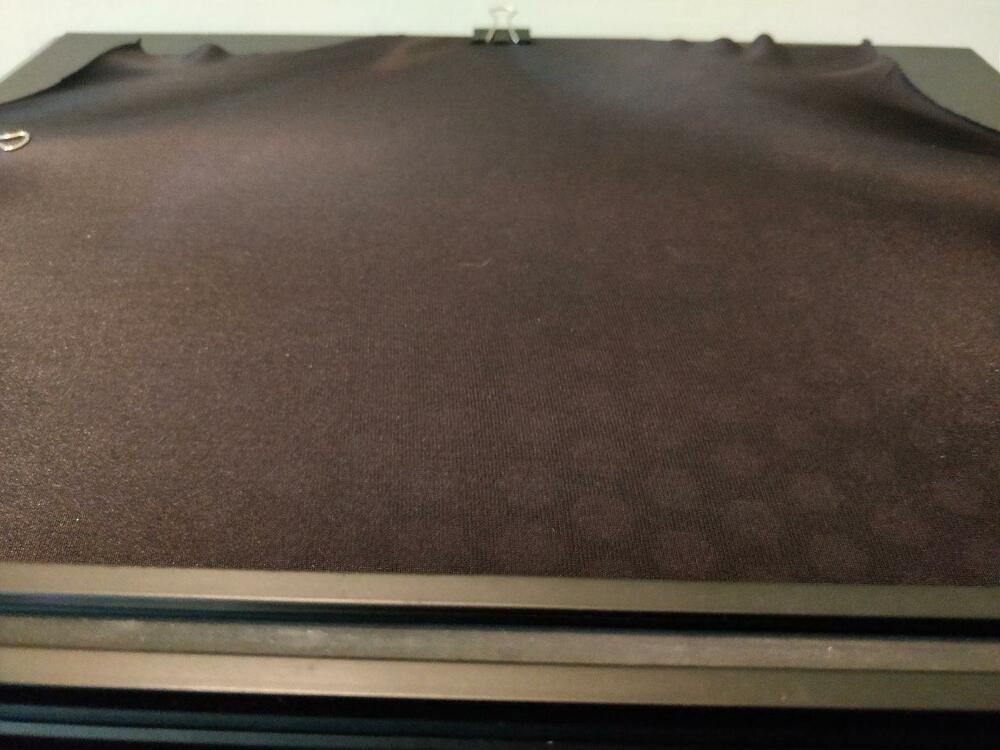
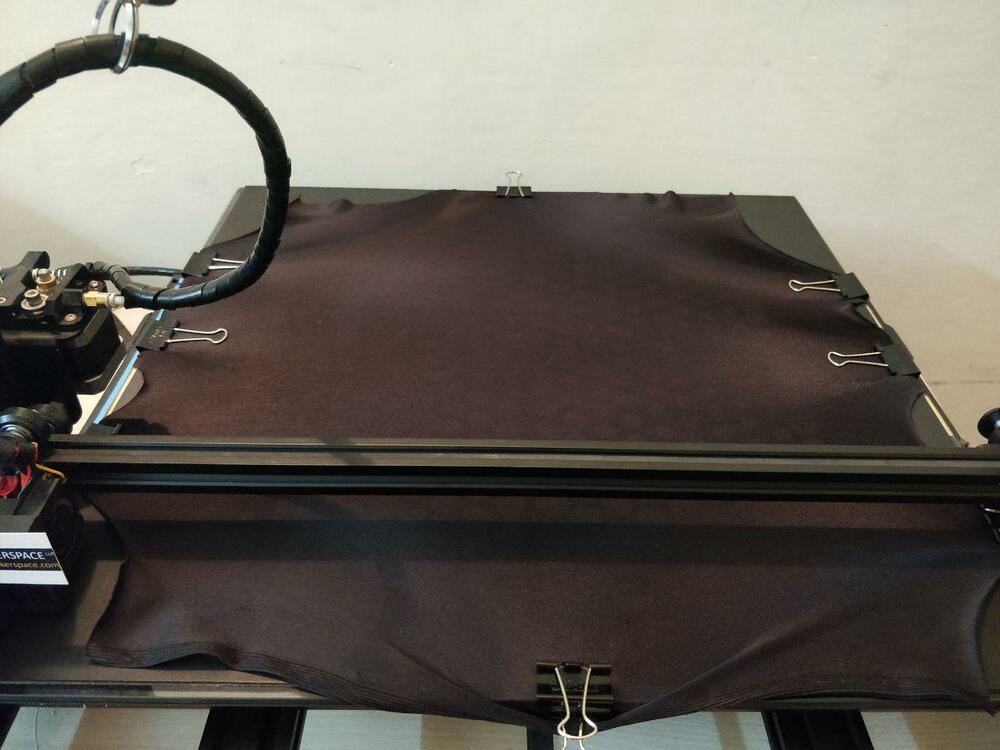
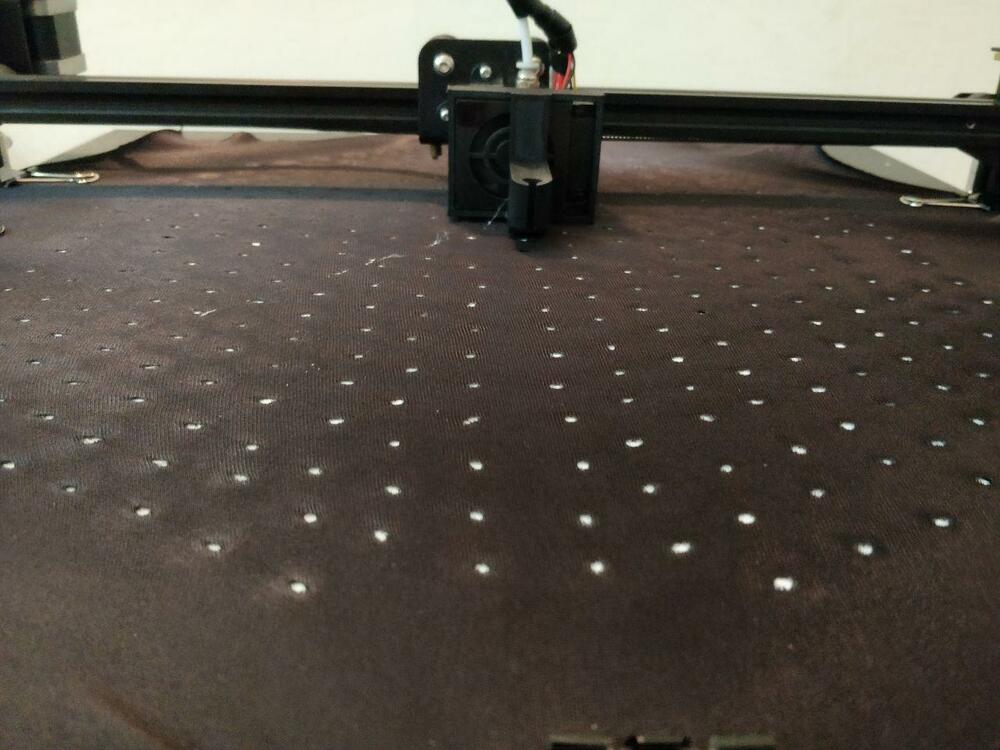
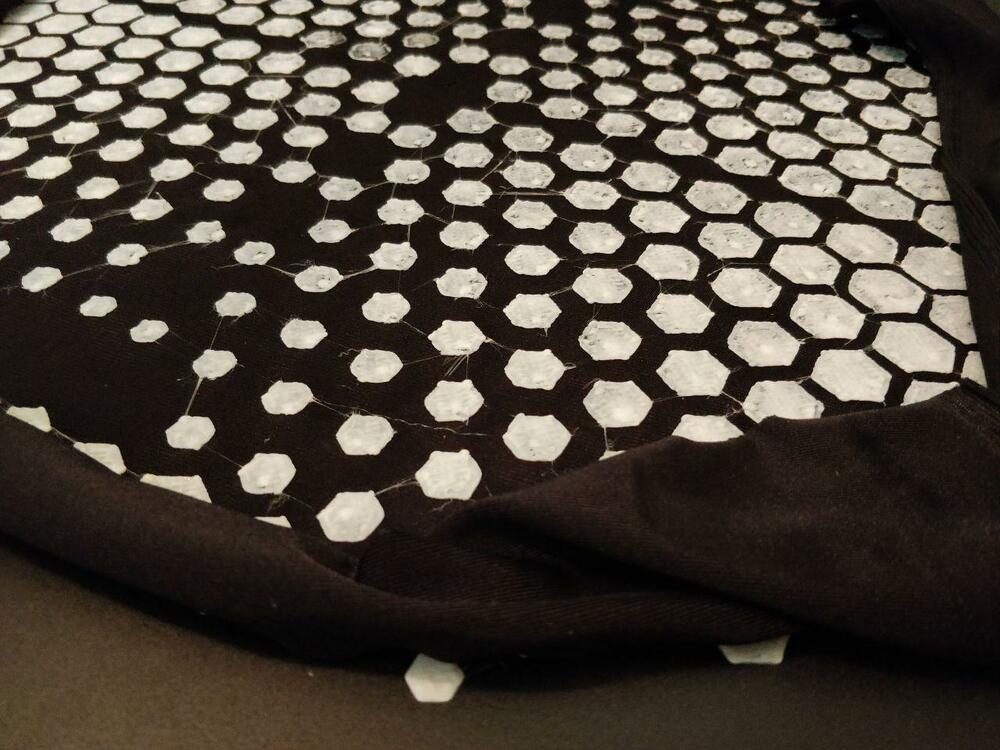
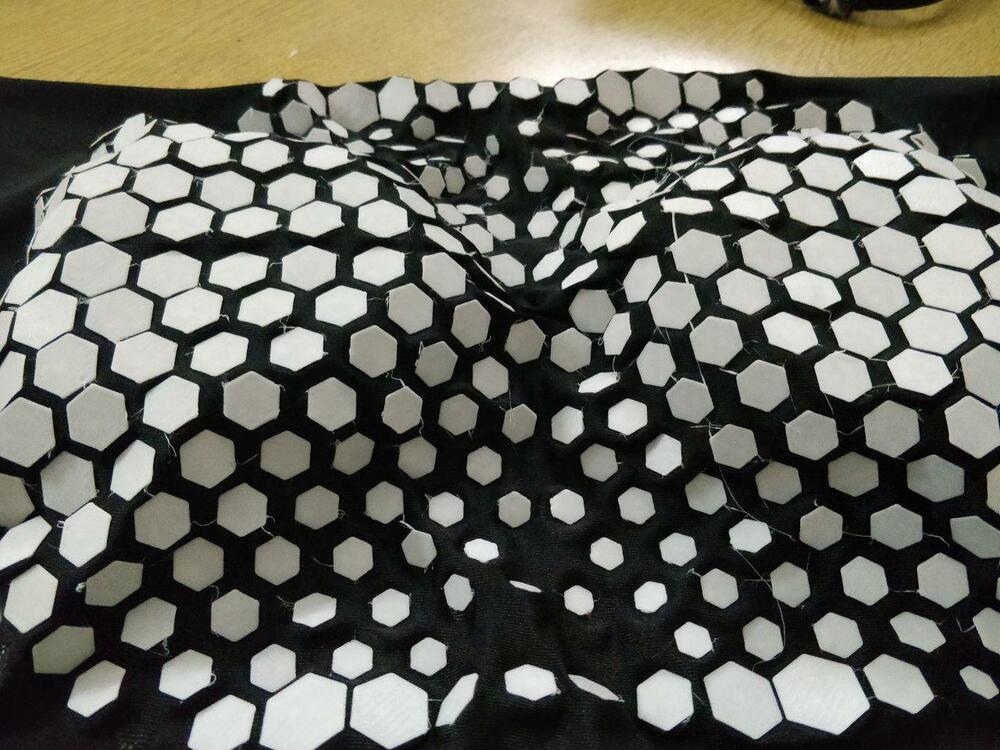
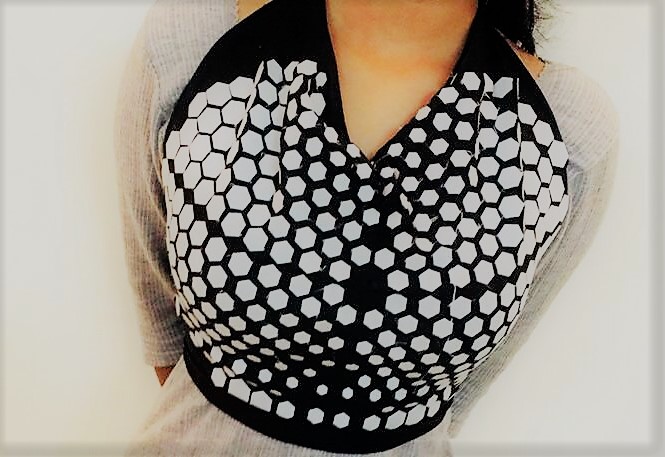
We have a couple of printers in the lab. The one we use for textile is an open bed one which makes it easier to use for this kind of a bigger design.
Printer Company: Creality 3D
Model: CR 10S5
Nozzle: 0.8mm (Brass)
Bed size: 505050 cm Volume
Material used: Plain PLA (Decomposable) - White & 4-way stretch Lycra
Below is a close image of the fabric which shows its a 4 way strect Black color Lycra. First I will print 2 layers on 3D printer and then clp this to bed.
Tempertaure set to 70 as its cold here and I didnt set extruder temperature as it immediately warms up when bed reches it temperature, plus we dont want extruder to start extruding till bed is ready.
Now,I am printing first layer, I have kept speed really slow, so that it sticks well and doest miss anything.
After two layers, I paused my printer and clipped Lycra, I clipped this on the bed by stretching it. You have to be careful while clipping that clips should not obstruct bed movement. This is an interesting week , majorly due to 3D printing, I really plan to make few Pieces post Fabricademy for displaying in our lab which involves 3D printing combined with Circular Design. Anyway, back to track.
You should be able to see the layer below because you will need to make some holes with air blower so that layer above sticks with below and they are well conencted, otherwise you will end up taking off only above layer which might come off when clips are opened. This Air blower experiment was tested by Mahavir while he did his assignment and i just learnt from his experiment and saved my time. The Video below, shows the whole process really well.
The purpose behind sharing this image was to show how I have clipped , I felt I still took a larger piece of cloth but I think thats ok untill its well stretch.
Finally after Air blowing, the printing starts, we can see through holes the layer below.
After opening clips,the layers are sticked to bed but when I took it off..it gave me what I wanted.
Well, this gives the perfect shape
We can see I used attractor points to spread my hexagons and after stretching how it took shape and easy to wear !